Industrial Switchgear Requirements: Essential Components for Plant Safety and Efficiency
Understand industrial switchgear requirements
An industrial plant use switchgear is virtually likely to require a comprehensive electrical power distribution system that ensure safety, reliability, and efficiency. Switchgear represent the central nervous system of industrial electrical infrastructure, control, protect, and isolate electrical equipment. Without proper switchgear components, manufacture facilities face increase risks of equipment damage, production downtime, and workplace hazards.
The specific requirements for industrial switchgear depend mostly on the facility’s size, production processes, and power demands. Nonetheless, certain fundamental components remain consistent across most industrial applications.
Circuit breakers: the primary protection mechanism
Industrial plants require robust circuit breakers as part of their switchgear setup. These devices mechanically interrupt electrical flow when faults are detected, prevent catastrophic equipment failure and potential fires.
Medium and high voltage circuit breakers in industrial settings typically utilize one of three interruption technologies:
-
Air circuit breakers (aacts)
Use for applications up to 15kv with current ratings up to 6300a -
Vacuum circuit breakers (vPCBs)
Common in medium voltage applications from 1kv to 38kv -
Sf6 (sulfur hexafluoride )circuit breakers
Prefer for higher voltage applications above 72.5kv
The selection depend on the specific voltage requirements, available space, maintenance capabilities, and environmental considerations of the facility. Modern industrial plants progressively favor vacuum circuit breakers for medium voltage applications due to their reliability, minimal maintenance needs, and environmental benefits compare to sf6 alternatives.
Protective relays and monitoring systems
Sophisticated protection relay systems represent another critical requirement for industrial switchgear. These devices incessantly monitor electrical parameters and trigger protective responses when abnormal conditions occur.

Source: techworldfull.blogspot.com
Modern industrial facilities typically implement microprocessor base protective relays that offer:
- Overcurrent protection
- Ground fault detection
- Differential protection
- Voltage monitoring
- Phase imbalance detection
- Data log capabilities
- Communication with plant wide control systems
The integration of these protective functions help prevent equipment damage while provide valuable diagnostic information for maintenance teams. Manufacture facilities with critical processes benefit from redundant protection schemes that ensure continuous operation regular if a primary protection system fail.
Power quality management solutions
Industrial plants with sensitive equipment and processes require power quality management as part of their switchgear system. Voltage fluctuations, harmonics, and power factor issues can damage equipment, reduce efficiency, and increase operational costs.
Power quality components usually integrate with industrial switchgear include:
-
Power factor correction capacitors
Reduce reactive power consumption and associate utility penalties -
Harmonic filters
Mitigate distortion cause by non-linear loads like variable frequency drives -
Surge protection devices
Shield sensitive equipment from voltage spikes -
Voltage regulators
Maintain consistent voltage levels despite supply fluctuations
Manufacture facilities with precision processes or automate equipment find these power quality solutions peculiarly valuable, as level minor electrical disturbances can result in product defects or production interruptions.
Remote monitoring and control capabilities
Modern industrial switchgear installations require advanced monitoring and control capabilities. Remote operation reduce exposure to arc flash hazards while provide comprehensive visibility into electrical system performance.
Key monitoring and control features include:
- SCADA (supervisory control and data acquisition )integration
- Real time power consumption analytics
- Predictive maintenance alerts
- Remote switching capabilities
- Historical trend analysis
- Automated reporting functions
These capabilities allow facility managers to identify potential issues before they cause downtime, optimize energy usage, and respond quick to electrical emergencies without place personnel at risk.
Arc flash protection systems
Industrial facilities must prioritize arc flash protection within their switchgear design. Arc flash incidents represent one of the virtually dangerous electrical hazards in industrial environments, capable of cause severe injuries or fatalities.
Modern arc flash protection requirements include:
-
Arc resistant switchgear enclosures
Contain and direct arc energy out from personnel -
Optical detection systems
Identify arc flash events within milliseconds -
High speed disconnection devices
Quickly isolate power when arcs are detected -
Remote rack mechanisms
Allow circuit breaker operation from safe distances -
Personal protective equipment (pPPE)protocols
Base on arc flash hazard analysis
Manufacture facilities with higher voltage requirements face increase arc flash risks, make these protective measures specially important for medium and high voltage switchgear installations.
Redundancy and reliability features
Continuous operation represent a critical priority for most industrial facilities, make redundancy a key requirement for switchgear systems. Redundant components and configurations ensure that single points of failure don’t result in complete production shutdowns.
Common redundancy approaches include:
-
Dual power feed
Multiple utility connections or on site generation -
Main tie main configurations
Allow power-sharing between separate bus sections -
Automatic transfer switches
Seamlessly transition between power sources -
Redundant protection schemes
Multiple layers of protective devices -
Spare parts inventory
Critical components maintain on site
The appropriate level of redundancy depend on the criticality of the industrial process and the cost implications of unexpected downtime. Facilities produce high value products or operate continuous processes typically implement more extensive redundancy measures.
Compliance with industry standards and regulations
Industrial switchgear must comply with numerous standards and regulations to ensure safety, reliability, and interoperability. These requirements vary by location but typically include:
-
ANSI / IEEE standards
Define performance requirements and testing procedures -
NFPA 70 (national electrical code )
Establishes installation requirements -
NFPA 70e
Addresses electrical safety in the workplace -
UL certifications
Verify equipment meet safety standards -
IEC standards
International requirements for electrical equipment
Manufacture facilities must ensure their switchgear not exclusively meet current requirements but can besides accommodate future regulatory changes through upgradeable designs and modular components.
Energy efficiency and sustainability features
Modern industrial plants progressively require energy efficient switchgear solutions that support sustainability goals while reduce operational costs. Energy management capabilities have become standard requirements for new switchgear installations.
Key energy efficiency features include:
-
Low loss transformers
Reduce energy waste through improve designs -
Smart metering
Provides detailed consumption data for optimization -
Energy management software
Identifies efficiency opportunities -
Peak demand control
Manages load to avoid demand charges -
Integration with renewable energy sources
Accommodate solar, wind, or other on site generation
These features not exclusively reduce environmental impact but besides provide significant cost savings through lower utility bills and improve operational efficiency.
Maintenance and serviceability considerations
Industrial switchgear require regular maintenance to ensure reliable operation throughout its service life. Maintenance friendly design features represent essential requirements for manufacturing facilities with limited downtime windows.

Source: micoope.com.gt
Important serviceability features include:
-
Draw out circuit breakers
Allow removal without DE energize entire sections -
Accessible connection points
Facilitate thermal scanning and connection tighten -
Modular components
Enable rapid replacement of fail parts -
Diagnostic ports
Support testing without dismantling -
Clear labeling and documentation
Improve maintenance efficiency
These features reduce maintenance costs while minimize the duration of plan outages, finally improve the total cost of ownership for the switchgear system.
Scalability and future proofing
Industrial facilities require switchgear solutions that can accommodate future expansion and technological advancements. Scalable designs prevent costly replacements as production needs evolve.
Future-proof considerations include:
-
Extra capacity
Size for anticipated load growth -
Expansion space
Physical room for additional sections -
Upgradable protection
Relay systems that accept firmware updates -
Communication protocols
Support for emerge network standards -
Interoperability
Compatibility with equipment from multiple manufacturers
These features ensure the switchgear investment remain viable throughout the expect operational lifetime of the industrial facility, typically 20 30 years for major electrical infrastructure.
Physical space and environmental requirements
Industrial switchgear installations have specific physical and environmental requirements that must be address during facility planning. These considerations impact both safety and performance.
Key spatial and environmental factors include:
-
Adequate clearances
Work space around equipment per electrical codes -
Ventilation and cool
Temperature management for optimal performance -
Floor loading capacity
Structural support for heavy equipment -
Fire protection systems
Appropriate for electrical equipment -
Environmental controls
Protection from dust, moisture, and contaminants
Manufacture facilities in harsh environments may require specialized switchgear with enhance protection against corrosive atmospheres, extreme temperatures, or high humidity levels.
Conclusion
An industrial plant use switchgear requires a comprehensive system that balance protection, reliability, efficiency, and compliance. The specific requirements vary base on the facility’s size, processes, and criticality, but the fundamental needs remain consistent: safe distribution of electrical power, protection of valuable equipment, and minimization of costly downtime.
As industrial processes become progressively automated and digitize, the role of switchgear continue to evolve from simple power distribution to intelligent power management. Modern manufacturing facilities benefit from switchgear solutions that not exclusively protect equipment but besides provide valuable operational insights through advanced monitoring and control capabilities.
When select switchgear for industrial applications, facility managers should consider not exclusively current requirements but besides future needs. The substantial investment in electrical infrastructure should support operational goals throughout the expected service life while adapt to change production demands, technological advancements, and regulatory requirements.
MORE FROM gowithdeal.com
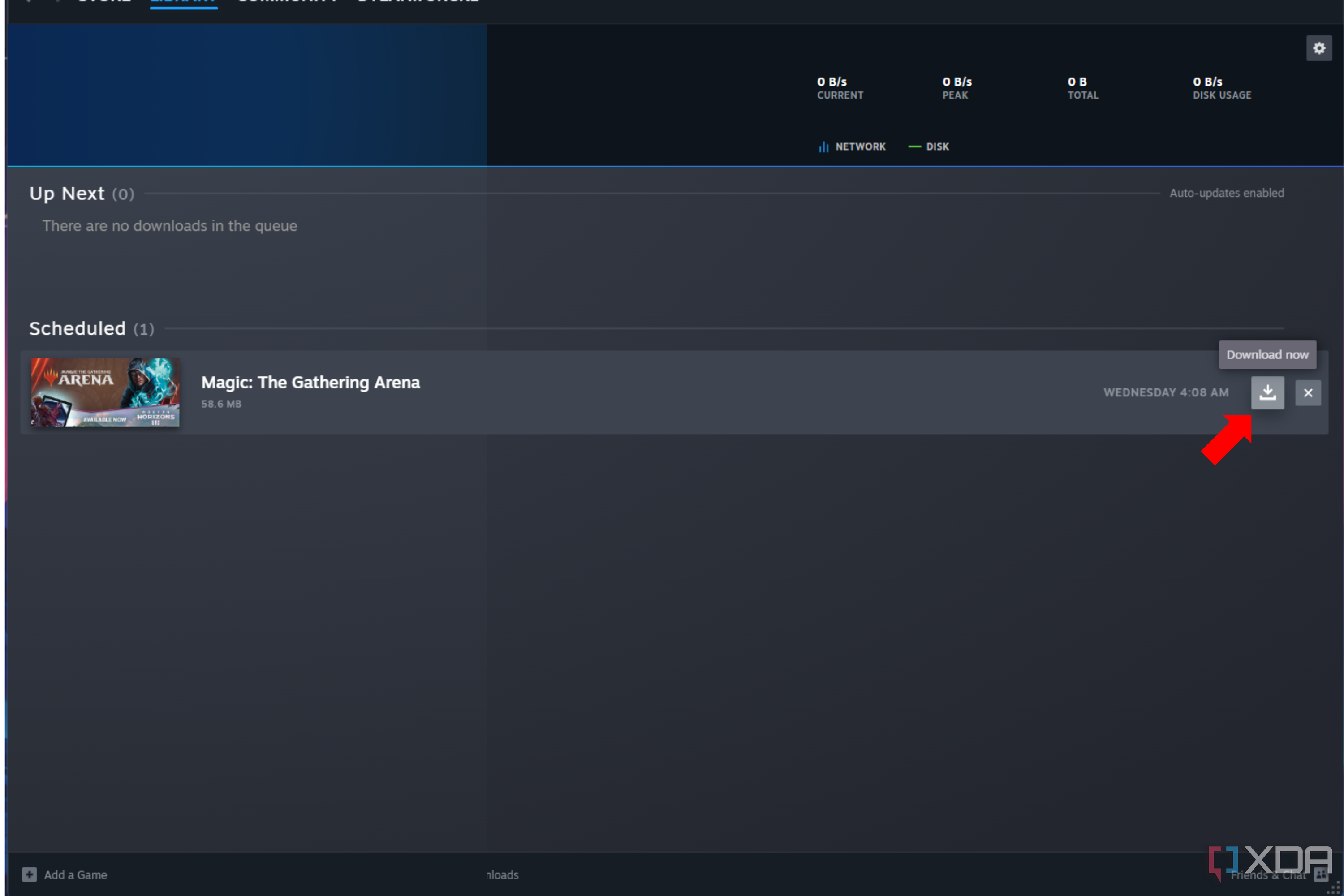
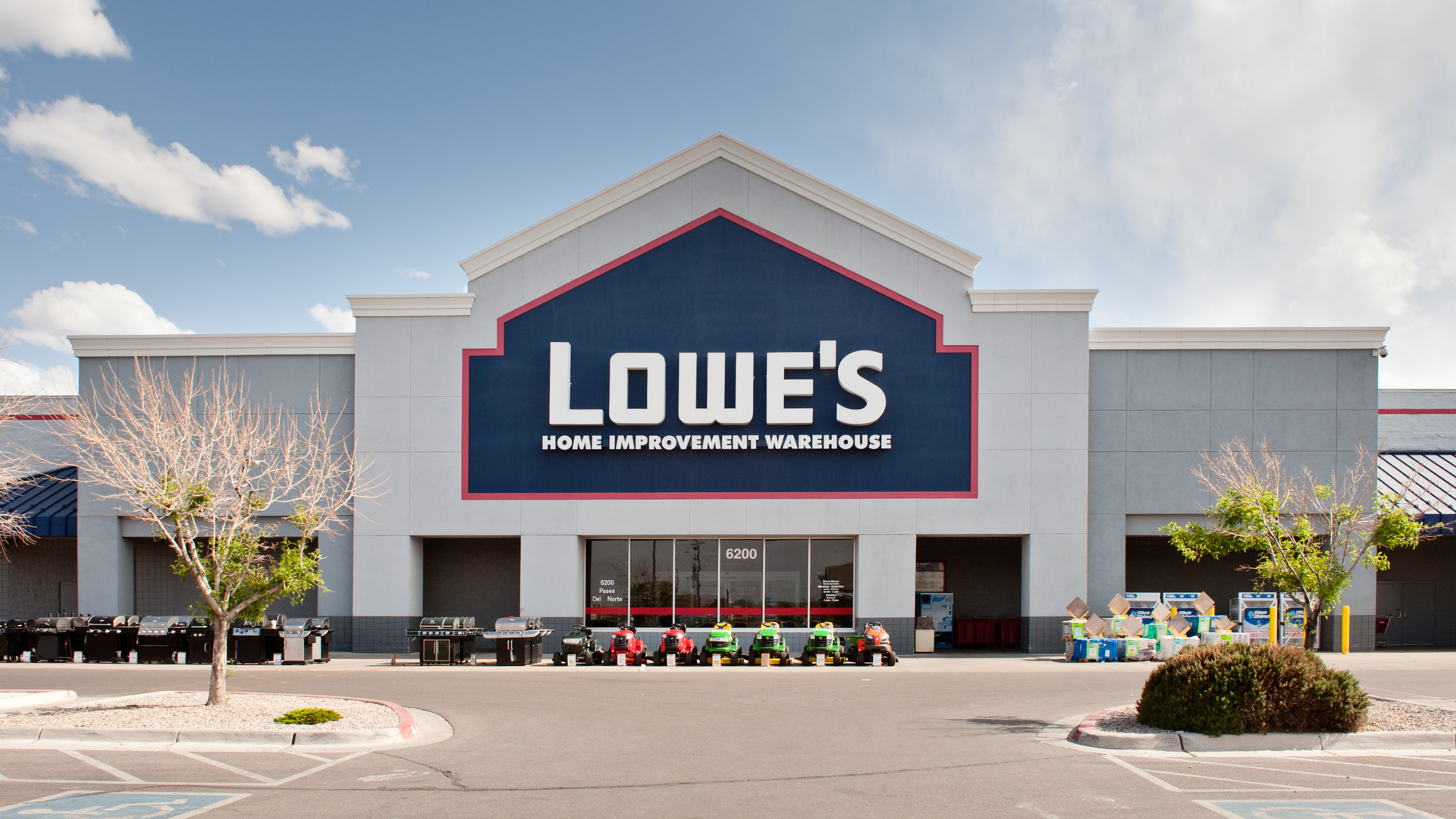
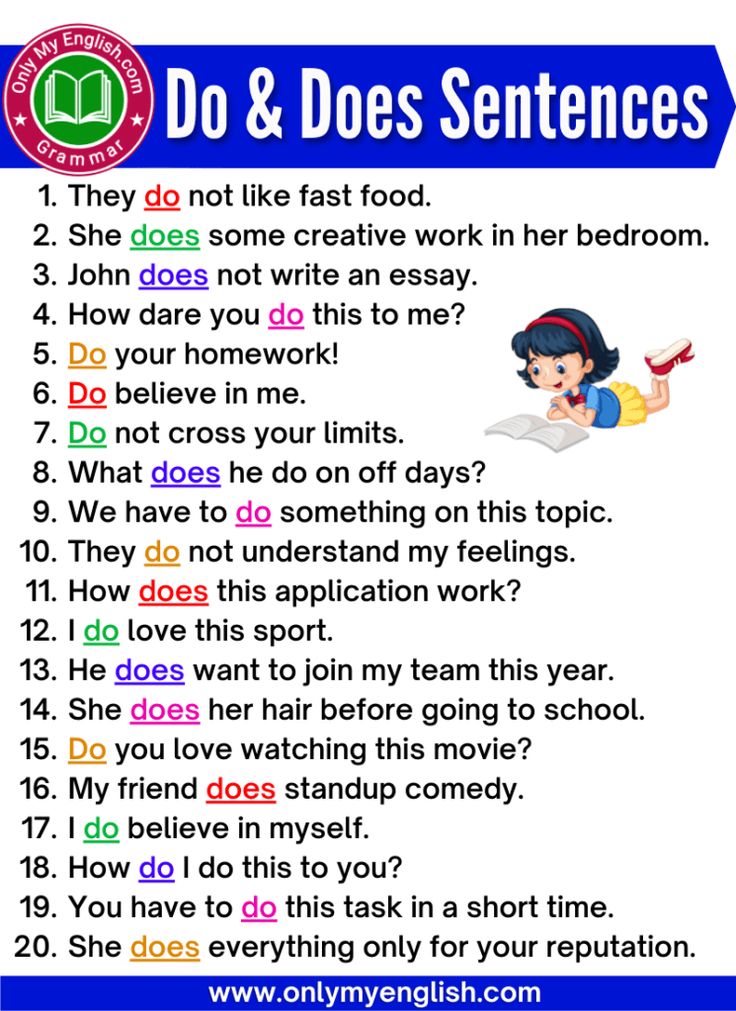
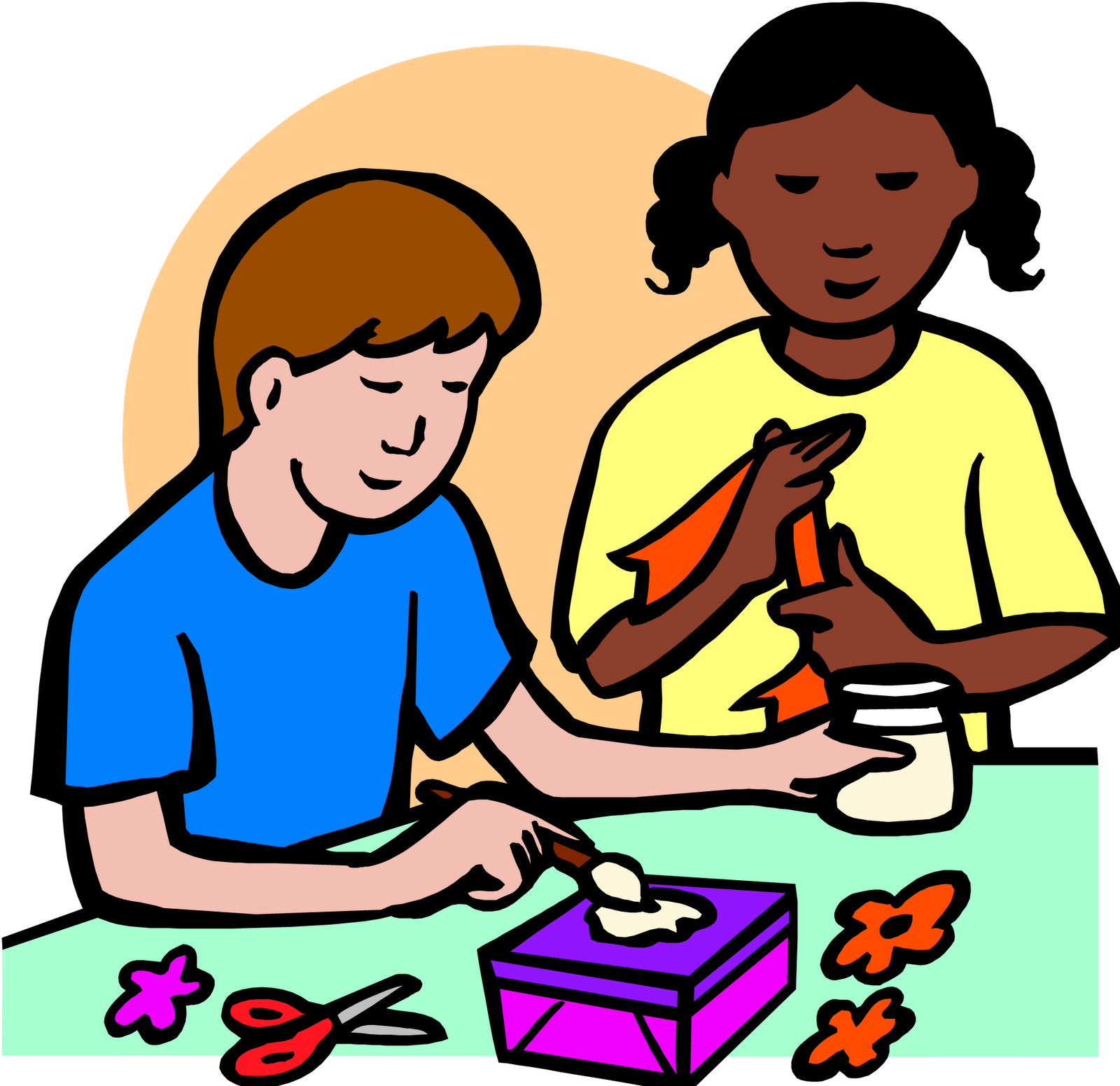
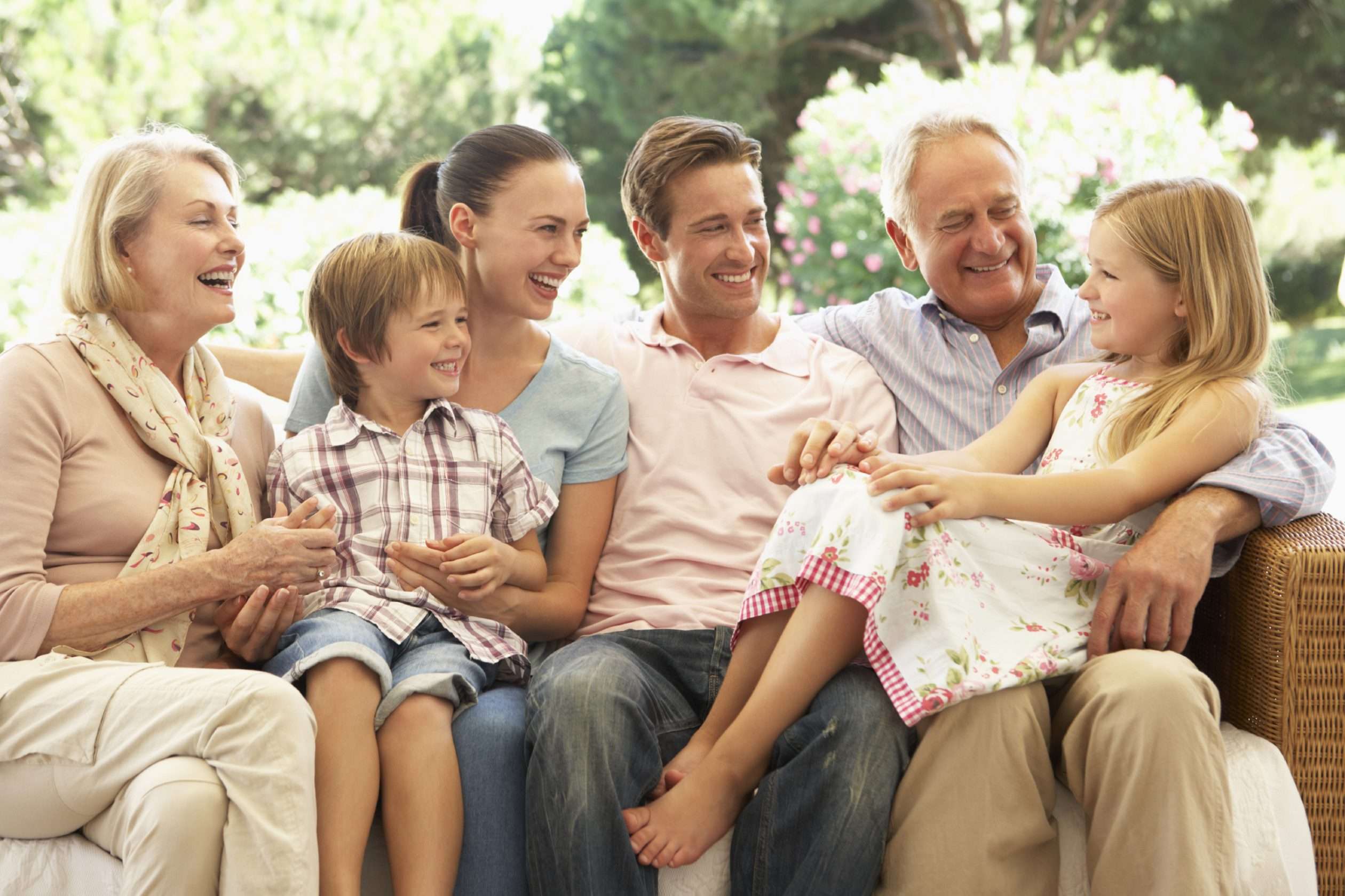
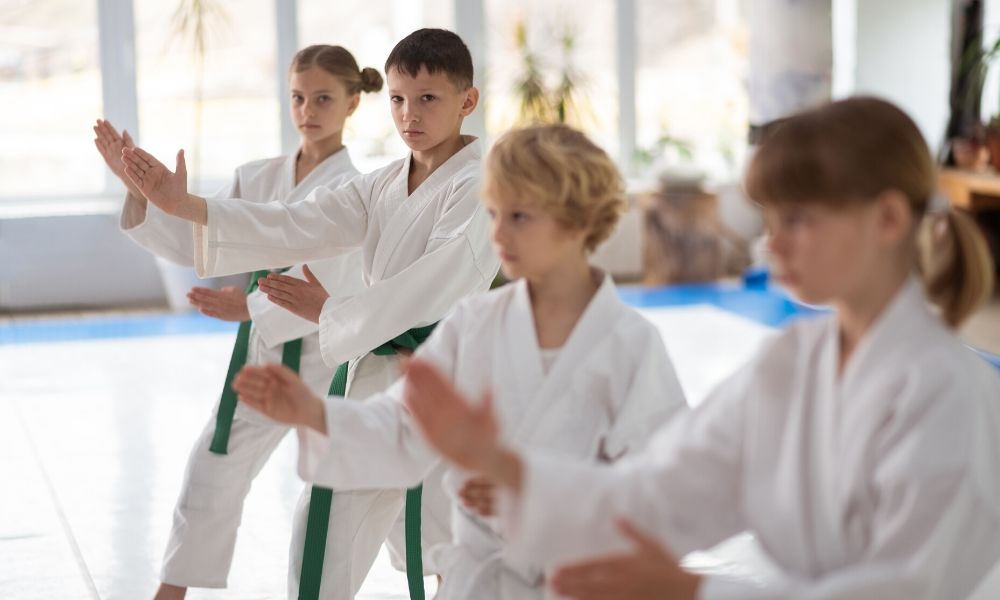
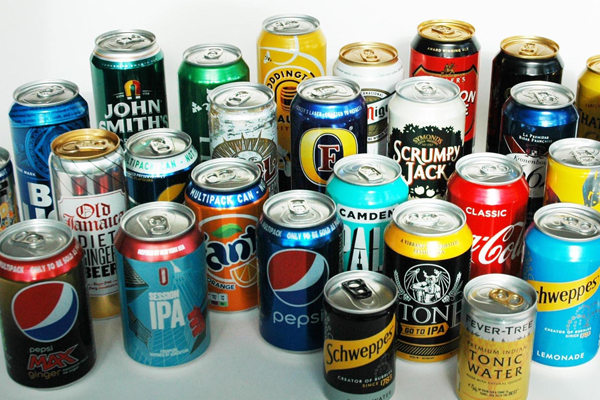
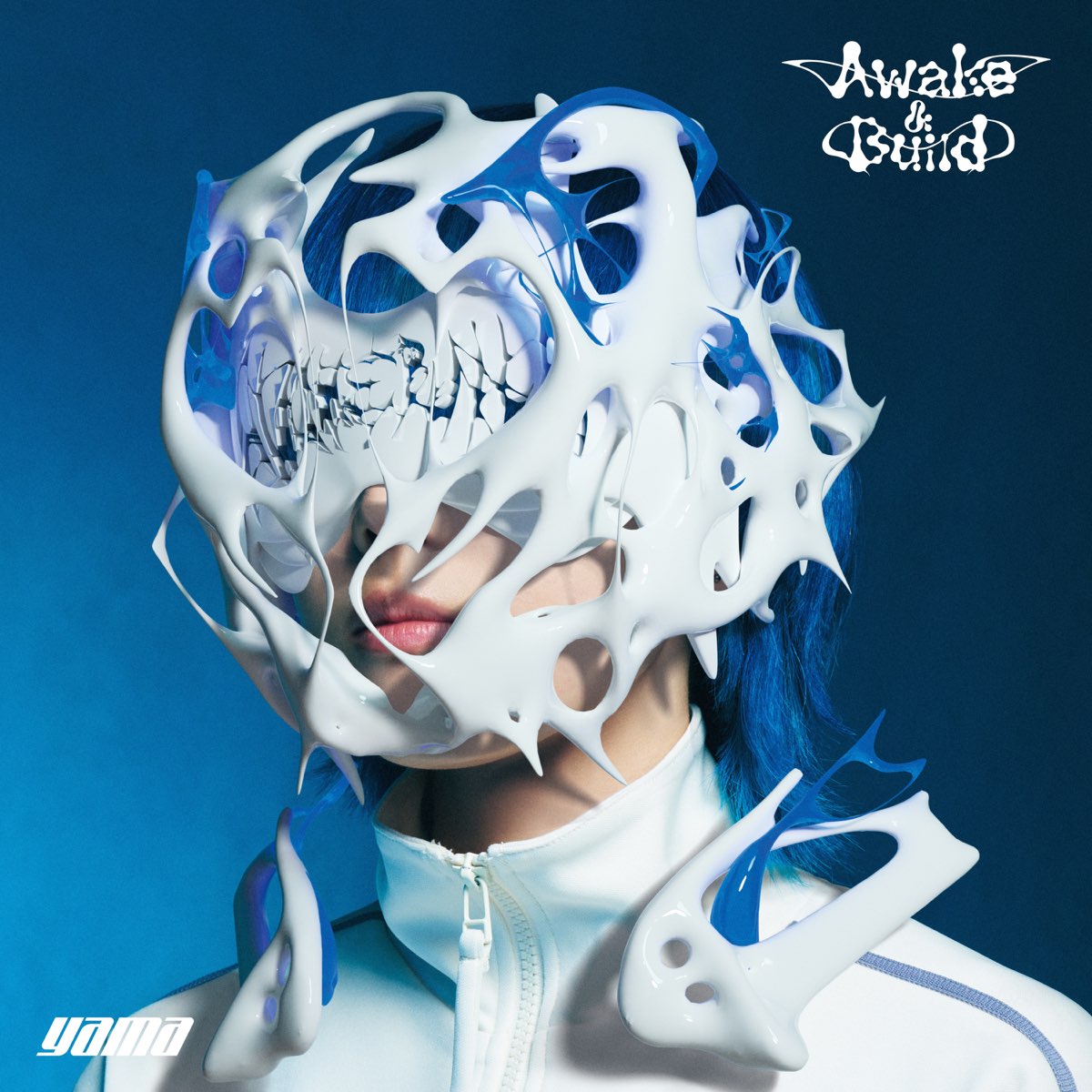
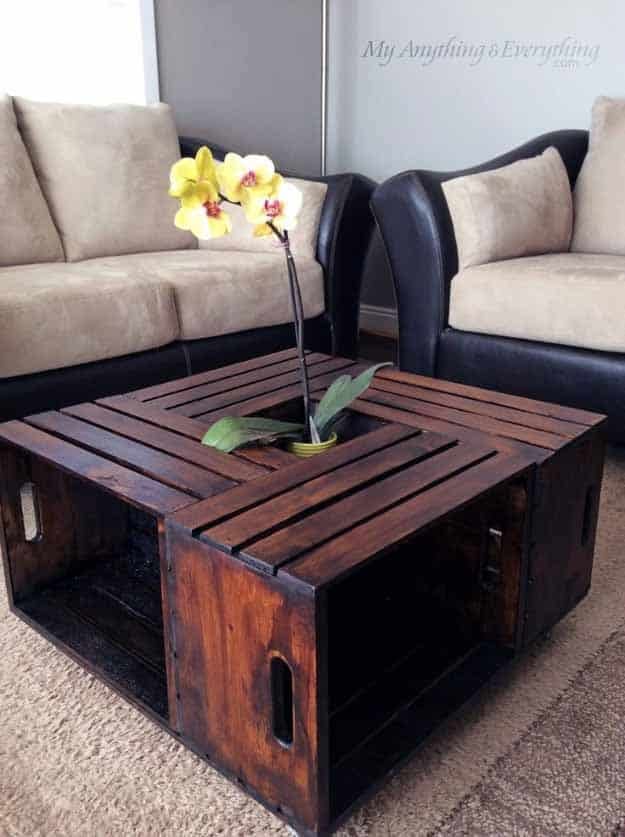
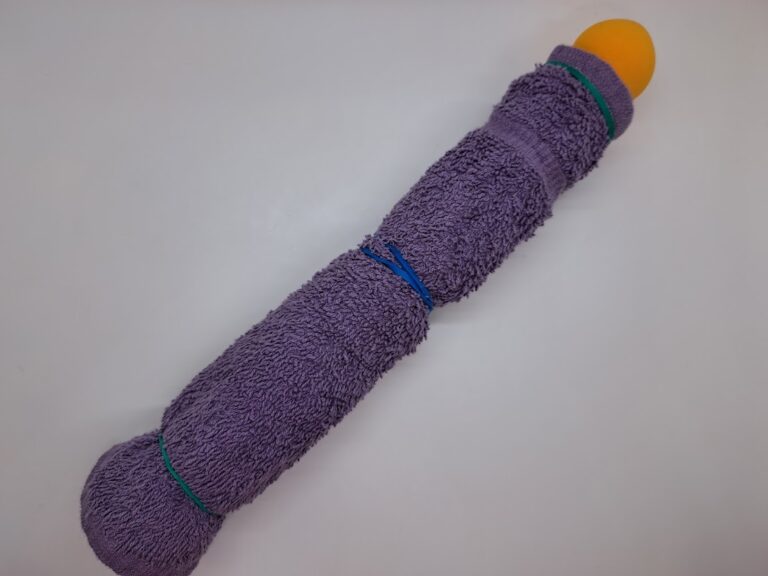
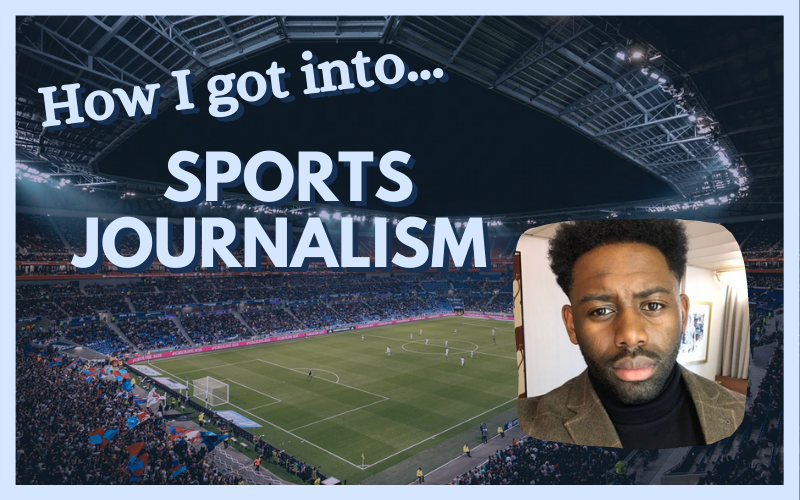
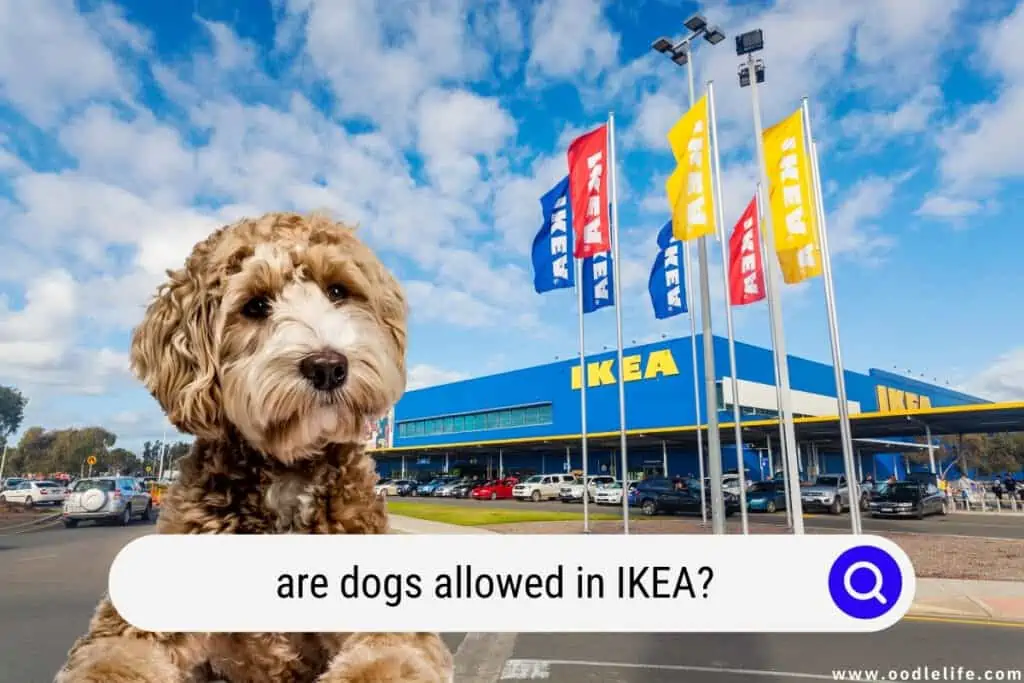