DIY Car Wrapping: Complete Guide to Transforming Your Vehicle at Home
Understand DIY car wrapping fundamentals
Car wrapping has revolutionized vehicle customization, offer an affordable alternative to expensive paint jobs. DIY car wrapping involve apply vinyl film to your vehicle’s exterior surfaces, create a new-look while protect the original paint underneath. This process require patience, proper tools, and technique, but deliver professional quality results when execute aright.

Source: dreamstime.com
Vinyl wraps come in countless colors, textures, and finishes, from matte black to chrome, carbon fiber patterns, and custom graphics. The material adheres to your car’s contours use heat and pressure, conform to curves and edges while maintain durability against weather and wear.
Essential tools and materials for success
Success in DIY car wrapping depend hard on have the right equipment. Professional grade vinyl wrap material form the foundation of your project. Choose high quality automotive vinyl from reputable manufacturers, as cheaper alternatives oftentimes fail untimely or prove difficult to work with.
Heat guns provide control temperature for activate the vinyl’s adhesive and make it pliable around curves. Squeegees and application tools help eliminate air bubbles and ensure proper adhesion. Sharp utility knives or precision cutting tools create clean edges and trim excess material.

Source: envocabulary.com
Surface preparation supplies include clean solvents, microfiber cloths, and tack cloths for remove contaminants. Primer pens help with edge sealing, while infrared thermometers monitor surface temperatures during application. Work gloves protect your hands and prevent fingerprints on the adhesive.
Vehicle preparation and surface assessment
Proper preparation determine the quality and longevity of your wrap installation. Begin by soundly wash your vehicle, remove all dirt, wax, and contaminants that could interfere with adhesion. Clay bars remove embed particles that regular washing can not eliminate.
Inspect your vehicle’s paint condition cautiously. Minor scratches and imperfections will telegraph through the vinyl, become visible in the finished wrap. Address significant damage before proceeding, as vinyl can not hide substantial flaws.
Remove badges, trim pieces, and accessories where possible. This allows for cleaner installation and advantageously look results. When removal isn’t feasible, plan your cutting and trim strategy cautiously to achieve professional look edges around these obstacles.
Choose an appropriate workspace with adequate lighting and temperature control. Ideal installation temperatures range between 68 78 degrees Fahrenheit, with low humidity levels. Dust free environments prevent contamination during the installation process.
Step-by-step installation process
Start your installation with flat, simple panels to build confidence and technique before tackle complex curves. The hood, roof, or trunk lid make excellent starting points for beginners. Measure and cut your vinyl pieces with about 4 6 inches of excess material on all sides for proper wrapping and tucking.
Position the vinyl cautiously before remove the backing paper. Many installers use the” hinge method, ” ecure one edge while gradually work across the panel. This prpreventshe vinyl from stick untimely in the wrong position.
Apply firm, consistent pressure with your squeegee, work from the center outwards to eliminate air bubbles. Maintain steady, overlap strokes to ensure complete adhesion. The vinyl should lay smooth and flat against the surface without wrinkles or trap air.
Heat application become crucial around curves and complex shapes. Warm the vinyl gradually, stretch it lightly to conform to the vehicle’s contours. Avoid overheating, which can damage the material or cause shrinkage late.
Mastering complex curves and challenging areas
Bumpers, mirrors, door handles, and wheel wells present the greatest challenges in DIY car wrapping. These areas require advanced techniques and extra patience to achieve professional results.
For deep curves and recesses, use relief cuts to prevent the vinyl from bunch or tear. Make small, strategic cuts that allow the material to lay flat without create visible seams. Heat help the vinyl stretch and conform to dramatic shape changes.
Door jambs require careful planning and execution. Wrap the vinyl into the jamb area sufficiently to prevent visible edges when doors are closed, but avoid excessive material that interfere with door operation or create unsightly bulges.
Mirrors and small protrude elements oftentimes require custom templates or multiple pieces for proper coverage. Take time to create precise patterns that minimize visible seams while ensure complete coverage.
Trim and finishing techniques
Professional look installations depend on clean, precise trimming. Use sharp blades and replace them oftentimes to prevent ragged cuts. Trim cautiously, leave slenderly more material than need, so refine your cuts gradually.
The” wrap and tuck ” ethod create clean edges by wrap vinyl around panel edges and secure it to hide surfaces. This technique eliminate visible cut lines and provide a factory like appearance.
Heat sealing edges help prevent lifting and ensure long term durability. Apply control heat while press edges unwaveringly against the surface. Primer pens can improve adhesion on difficult surfaces or edge areas.
Post installation heating, frequently call” post heating, ” ctivate the adhesive full and relieve stress in the vinyl. This process help prevent lifting and improve the wrap’s longevity.
Common mistakes and how to avoid them
Air bubbles represent the virtually common issue in DIY installations. Most small bubbles can be work out during installation use proper squeegee technique. Persistent bubbles may require prick with a fine needle and work the air out cautiously.
Overstretch vinyl cause premature failure and lifting. Work with the material’s natural properties instead than force it into position. Proper heating make vinyl more pliable without require excessive stretching.
Contamination during installation create adhesion problems and visible defects. Maintain clean hands, tools, and work surfaces throughout the process. Remove any debris instantly if it contacts the adhesive.
Poor edge work create lift and premature failure. Ensure all edges are right heat, press, and seal. Expose adhesive attract dirt and lead to edge lifting over time.
Maintenance and longevity
Proper care extend your DIY wrap’s lifespan importantly. Handwashing with mild soap prevents damage from harsh chemicals or high pressure sprays. Avoid automatic car washes, which can catch and lift edges or corners.
Regular inspection helps identify potential problems other. Address lift edges instantly use heat and pressure to re-activate the adhesive. Small repairs prevent larger failures that might require panel replacement.
UV protection help prevent fading and material degradation. Park in shade areas when possible, and consider ceramic coatings design specifically for vinyl wraps to enhance protection and appearance.
Quality vinyl wraps typically last 5 7 years with proper care, make DIY installation a cost-effective long term investment in your vehicle’s appearance.
Cost analysis and time investment
DIY car wrapping offer substantial savings compare to professional installation. Material costs for a complete vehicle wrap typically range from $500 1500, depend on vinyl quality and vehicle size. Professional installation much cost $$30005000 for the same project.
Time investment vary importantly base on experience level and vehicle complexity. First time installers should expect 20 40 hours for a complete vehicle wrap, while experience divers might complete the same project in 10 15 hours.
Consider the learning curve when plan your project timeline. Start with smaller sections or partial wraps help build skills before attempt complete vehicle transformations.
When to consider professional help
While DIY car wrapping is achievable for motivated individuals, certain situations warrant professional installation. Passing complex vehicles with numerous curves and details challenge eventide experienced divers.
Commercial applications or show vehicles oftentimes require the precision and warranty backing that professional installers provide. Time constraints might besides make professional installation more practical despite the higher cost.
Insurance considerations may influence your decision. Some policies provide coverage for professional installations but exclude DIY work from protection.
DIY car wrapping represent an exciting opportunity to transform your vehicle while develop valuable skills. Success require patience, proper preparation, and quality materials, but the results can rival professional installations. Whether you choose a subtle color change or dramatic custom graphics, the satisfaction of complete this challenging project yourself make the investment in time and effort worthwhile. With careful planning and attention to detail, your DIY wrap will provide years of enjoyment while will protect your vehicle’s original finish.
MORE FROM gowithdeal.com
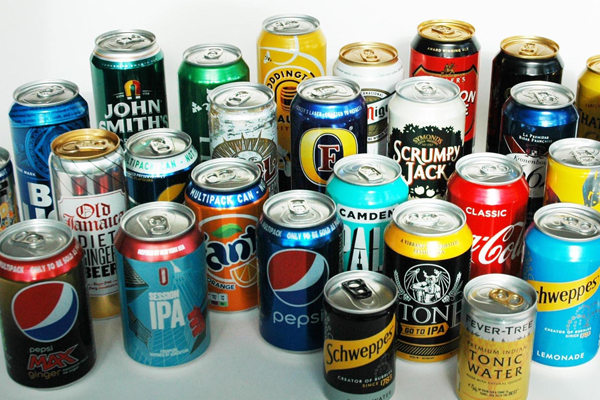
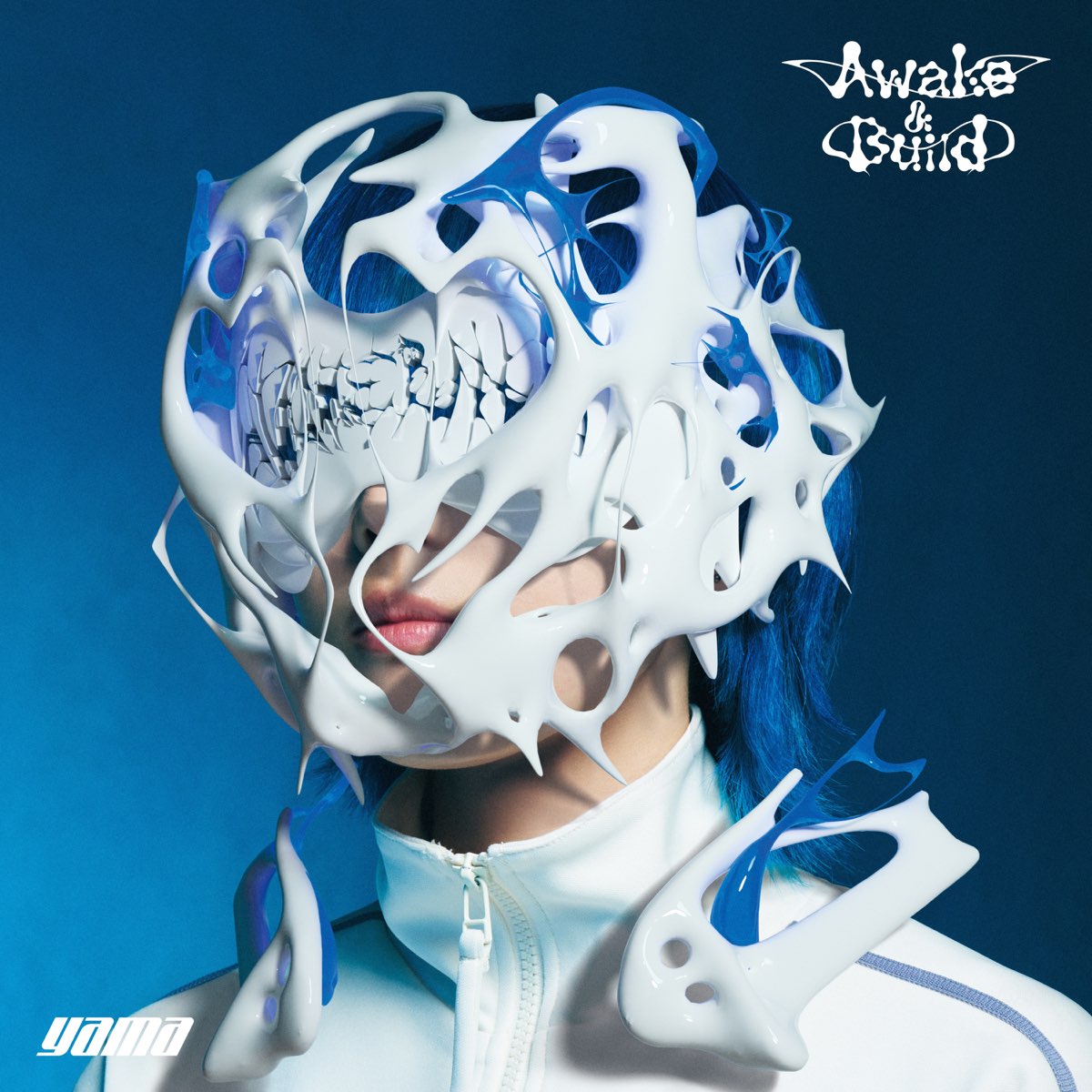
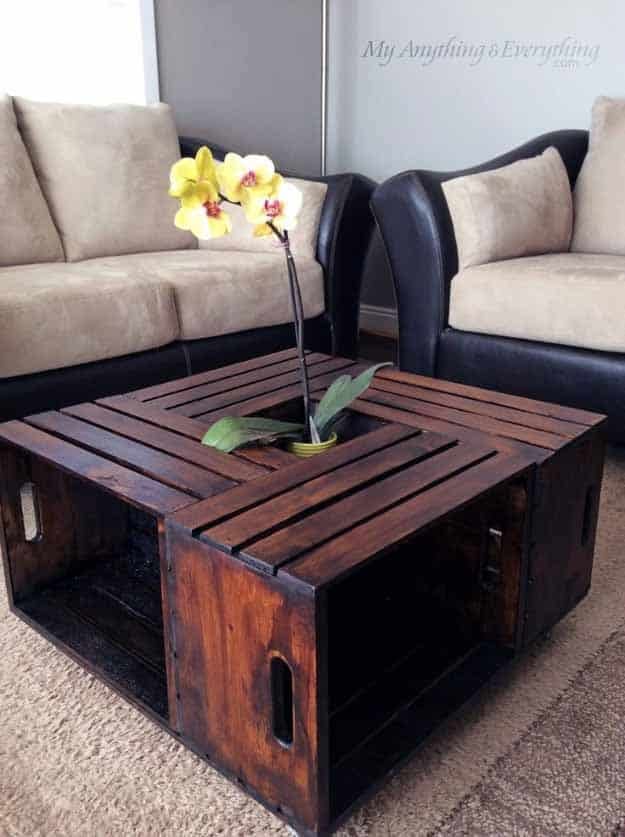
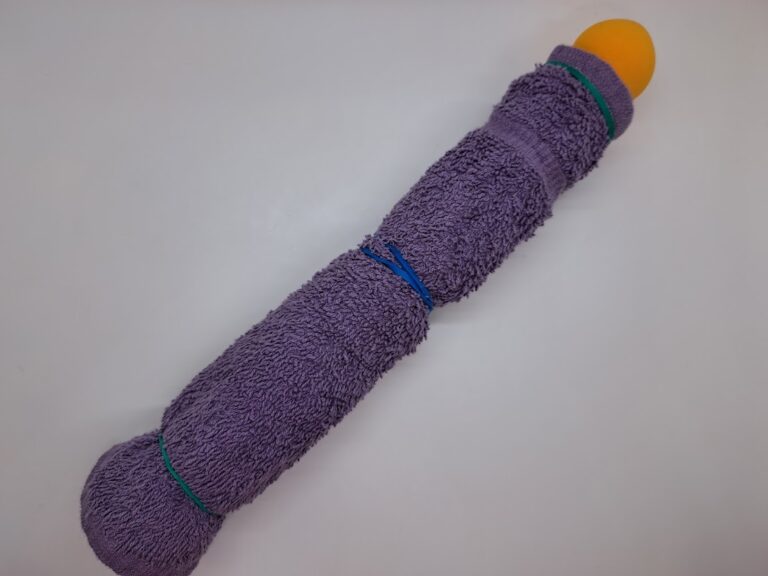
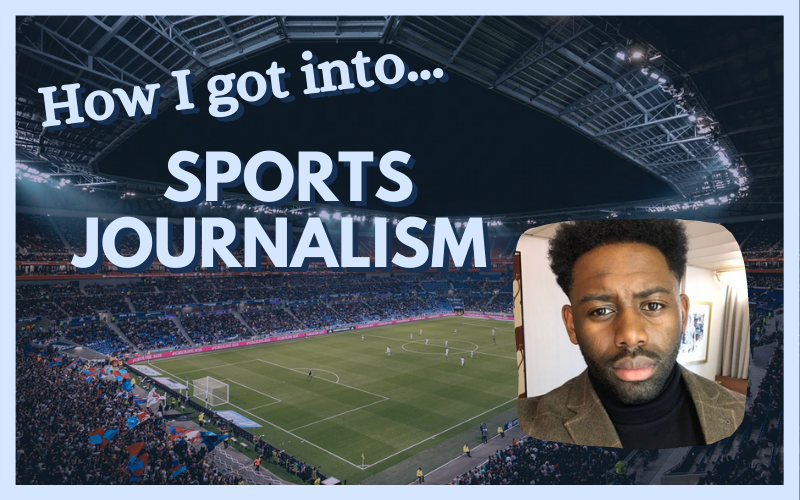
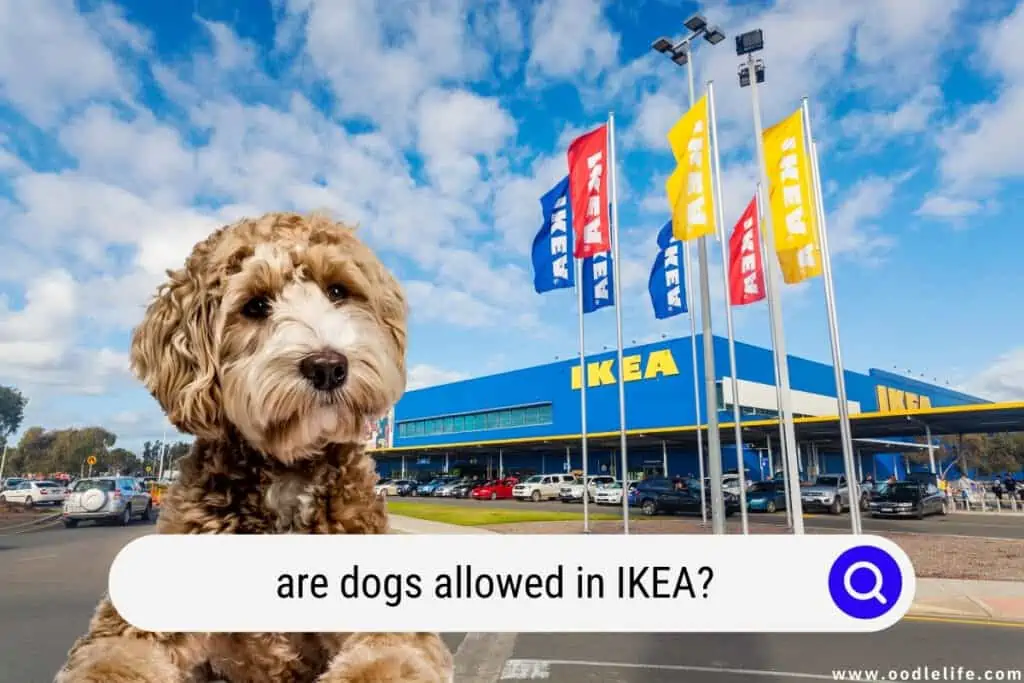
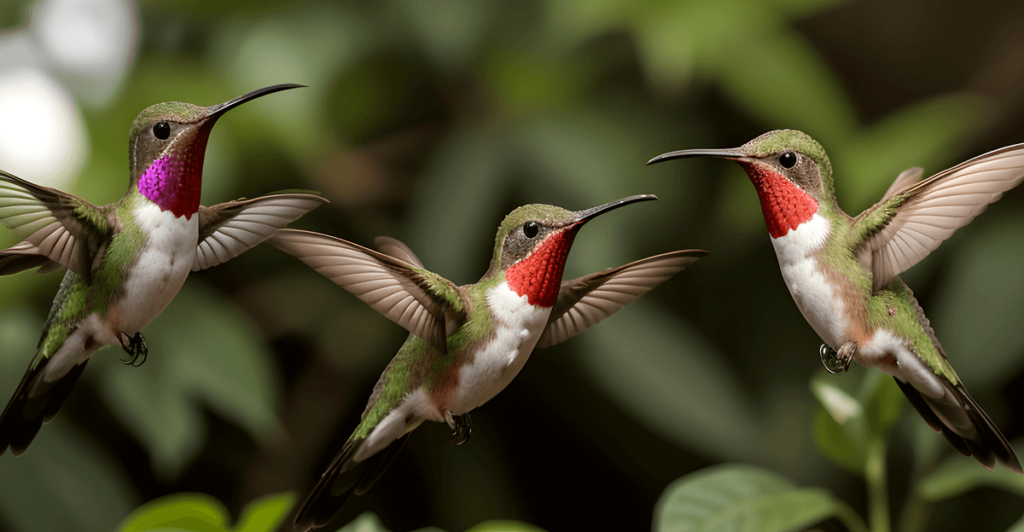
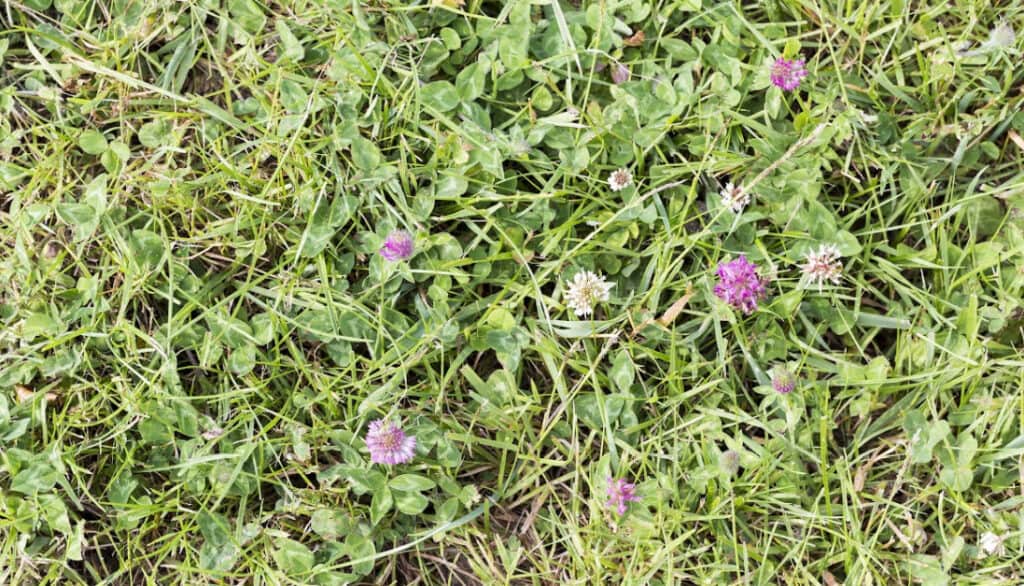
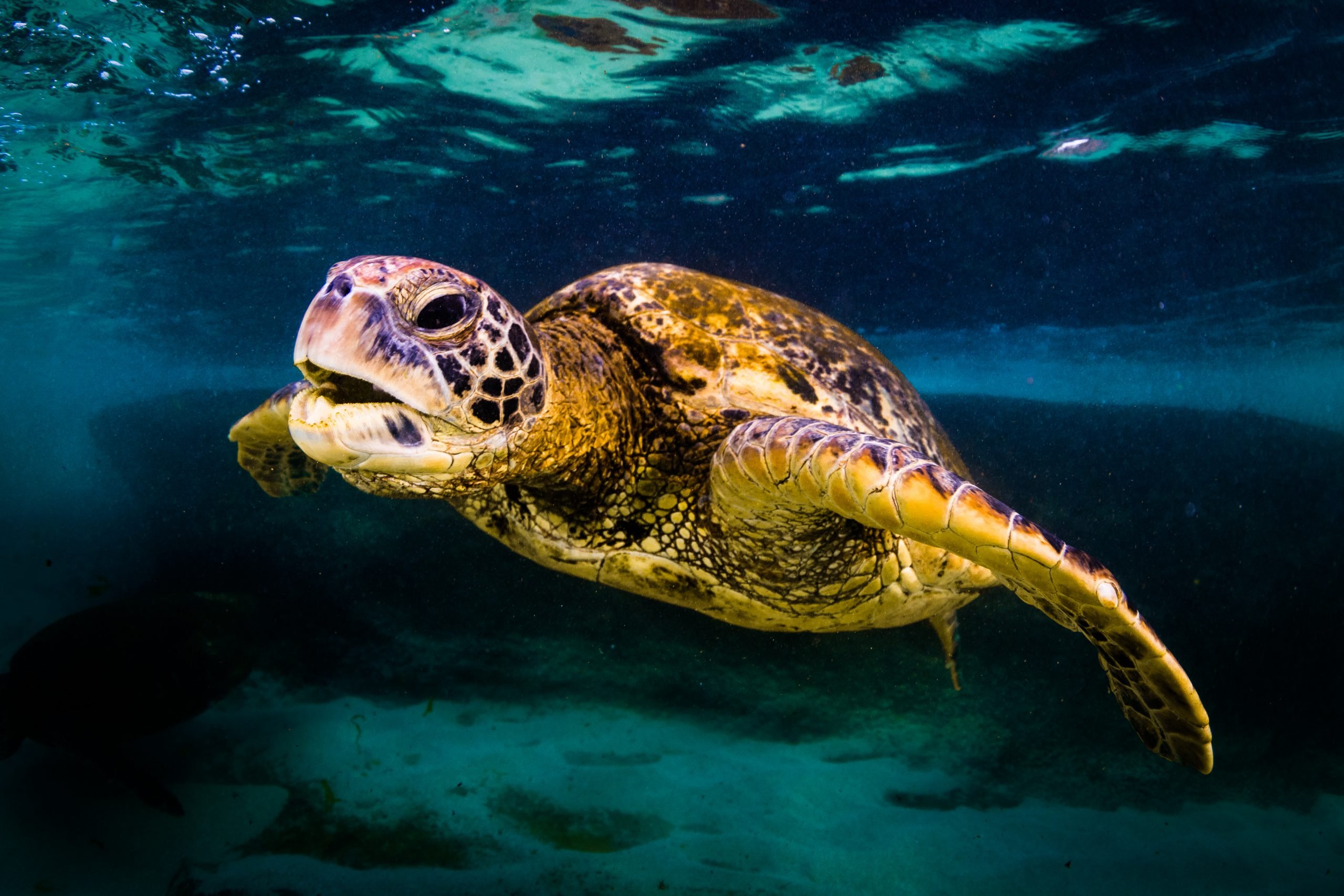
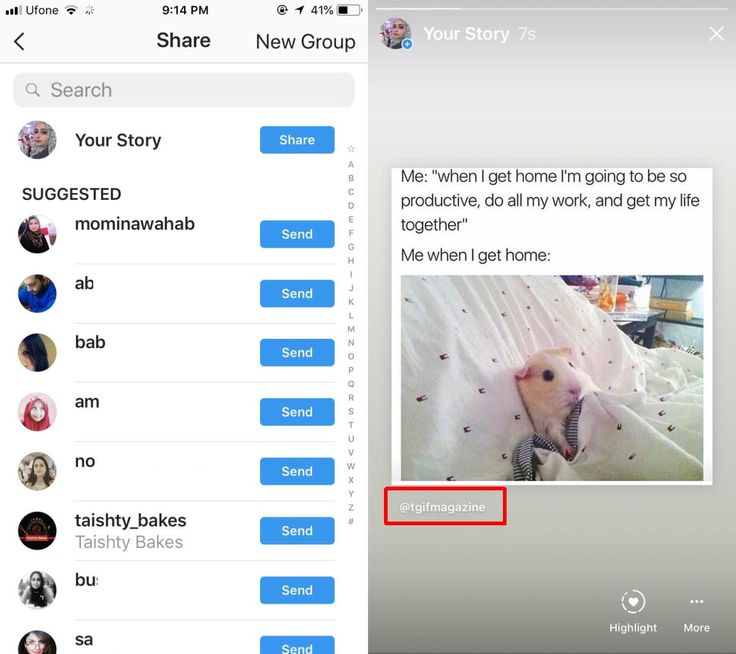
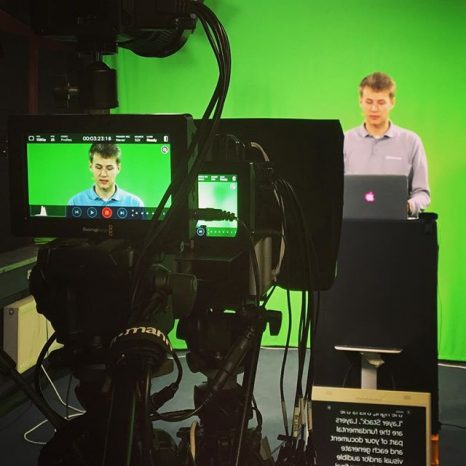
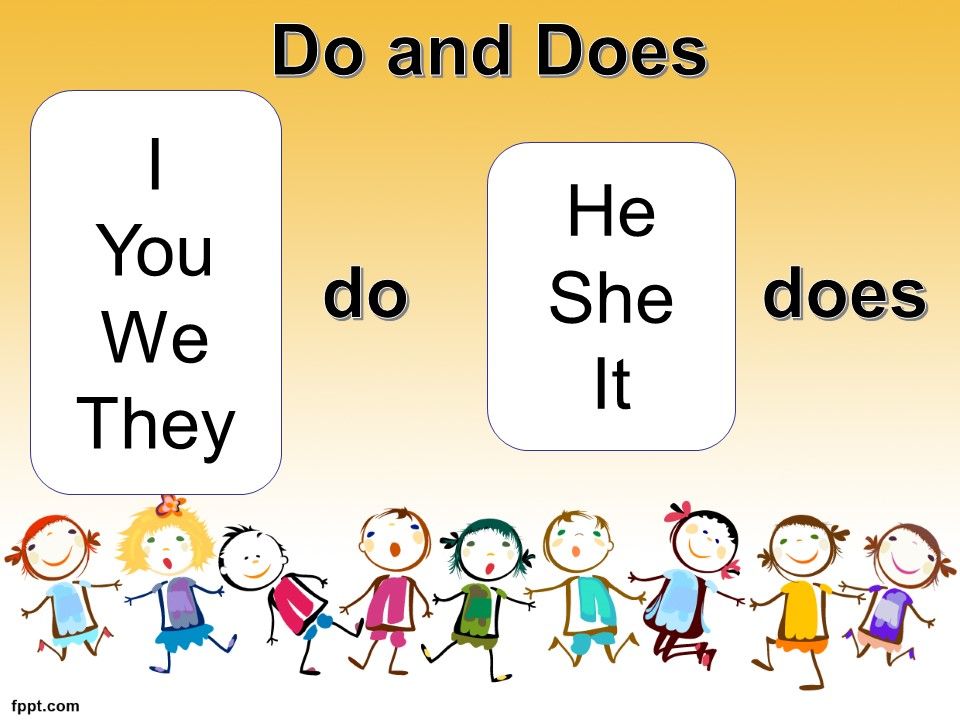