Understanding PDI in Automotive: The Role and Importance of Pre-Delivery Inspection
What Does PDI Stand for in Automotive?
PDI in the automotive sector stands for Pre-Delivery Inspection . This is a systematic and comprehensive procedure performed by dealerships or manufacturers before a vehicle is handed over to the customer. The aim is to guarantee that the vehicle arrives in perfect working order, free from defects, and ready for the road. The PDI process is an industry-standard practice, considered essential for maintaining quality and customer satisfaction [1] [2] .
The PDI Process: Key Steps and Checks
The PDI involves a thorough inspection of a vehicle’s mechanical, electrical, and cosmetic systems. While the specific procedures may vary by manufacturer and dealership, the core steps include:
- Exterior Inspection: Technicians check the paintwork for scratches, dents, or imperfections. They also inspect the body lines for gaps and make sure all exterior components-such as lights, mirrors, and trim-are properly fitted [1] [5] .
- Interior Examination: The interior is checked for cleanliness, damage, and correct installation of features. All electrical systems-such as infotainment, air conditioning, and seat adjustments-are tested for proper operation.
- Mechanical and Safety Checks: Fluid levels (engine oil, coolant, washer fluid), tire pressure, and battery charge are verified. Essential safety features like seatbelts, airbags, and dashboard warning lights are checked for functionality [3] .
- Operational Test: A brief test drive may be conducted to detect any mechanical issues, noises, or dashboard warnings. This step ensures the vehicle operates as intended and is safe to drive.
- Final Detailing: The vehicle is cleaned inside and out to ensure a pristine presentation for the customer.
Some manufacturers conduct PDI at centralized depots before shipping to dealers, while others have the dealership perform the inspection upon arrival [1] . Regardless of location, trained technicians with expertise in the vehicle’s systems perform these inspections.

Source: es.learniv.com
Why Is PDI Important?
The Pre-Delivery Inspection is not just a formality; it is vital for several reasons:
- Ensuring Vehicle Quality: PDI helps identify and resolve any issues that may have arisen during manufacturing or transportation, such as minor mechanical faults, cosmetic blemishes, or missing accessories [4] .
- Customer Satisfaction: Completing a thorough PDI reduces the risk of post-delivery complaints and warranty claims, helping build trust and satisfaction for new car owners.
- Safety Assurance: By checking operational and safety-critical systems, the dealership ensures the vehicle meets regulatory standards and is safe to drive off the lot.
- Dealership Reputation: Dealerships with rigorous PDI processes enjoy better customer feedback and fewer returns or issues after delivery. Some manufacturers, like Hyundai, enforce strict PDI protocols to maintain high satisfaction and reward dealers accordingly [4] .
What Happens If Issues Are Found During PDI?
If technicians discover any faults-mechanical, cosmetic, or electronic-during the PDI, these are documented and corrected before delivery. Repairs might include fixing minor scratches, replacing faulty bulbs, topping up fluids, or recalibrating systems. Only after the vehicle passes all checks is it cleared for handover to the customer [2] .
PDI for New vs. Used Vehicles
While PDI is most commonly associated with new vehicles, reputable dealerships also perform similar checks on used vehicles. For used cars, the process may involve a more comprehensive inspection and additional repairs or maintenance as needed. This ensures the vehicle is roadworthy and meets a dealer’s quality standards before being offered for sale [4] .
How Can Buyers Participate in the PDI Process?
Buyers are encouraged to be present during the PDI process when possible. This allows you to:
- Observe the inspection and ask questions about the vehicle’s features and operation
- Verify that all accessories and documentation (owner’s manual, spare key, warranty papers) are included
- Request clarification or immediate correction if any issues are identified
If attending in person is not feasible, you can ask the dealership for a detailed PDI checklist and confirmation that all items have been addressed. It is also advisable to conduct a personal walkaround and test of the vehicle before signing final delivery documents [5] .
Step-by-Step Guidance: Ensuring a Successful PDI
- Before Delivery: Contact your dealership and ask for their specific PDI checklist. Request to be present during the inspection, if possible.
- During PDI: Observe as technicians check the vehicle’s exterior, interior, and mechanical systems. Bring up any concerns immediately.
- Documentation: Ensure all manuals, service books, warranty cards, and keys are provided. Confirm that the vehicle’s registration and title are in order.
- Final Review: Perform your own walkaround and test features like lights, locks, infotainment system, and climate control. Take a brief test drive with the dealer’s permission.
- After Delivery: If you notice any issues after taking possession, promptly contact the dealership to arrange for correction under warranty or delivery guarantees.
This process helps you avoid future hassles and ensures you receive your new vehicle in the best possible condition.
Potential Challenges and Solutions
Some buyers may find it challenging to coordinate attendance at the PDI or may feel uncertain about what to inspect. In these cases, consider the following alternatives:
- Request a copy of the completed PDI checklist from your dealer and review it carefully.
- Ask a trusted mechanic or knowledgeable friend to accompany you for an independent check.
- Use online resources or manufacturer guides to familiarize yourself with common PDI items for your specific vehicle make and model.
If post-delivery issues arise, contact the dealership immediately. Most new cars come with comprehensive warranties, and reputable dealers will address legitimate concerns.

Source: confusedwords.org
How to Access Additional Resources on PDI
For more information on Pre-Delivery Inspection and its importance, consider the following steps:
- Visit your vehicle manufacturer’s official website and search for “pre-delivery inspection” or “PDI checklist” for guidance specific to your make and model.
- Consult your dealership’s service department for details on their PDI process and standards.
- Explore automotive education resources and consumer car-buying guides to better understand your rights and best practices related to PDI.
- If you have concerns about PDI quality or dealership practices, you may contact your local consumer protection agency or the Better Business Bureau for assistance.
Summary and Key Takeaways
In summary, PDI (Pre-Delivery Inspection) is a vital step in the automotive sales process, designed to ensure that every vehicle meets quality and safety standards before reaching the customer. By understanding the PDI process and participating actively, buyers can help safeguard their investment, prevent future problems, and enjoy greater peace of mind with their new purchase. Dealerships and manufacturers alike benefit from robust PDI practices through improved customer satisfaction and reputation in the market.
References
MORE FROM gowithdeal.com
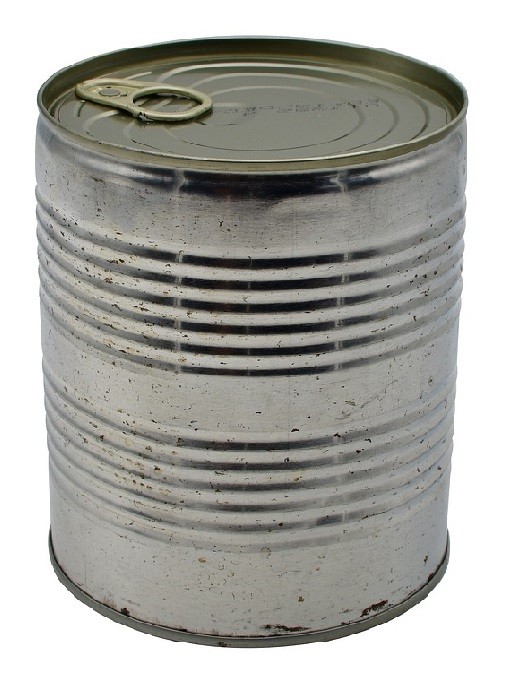
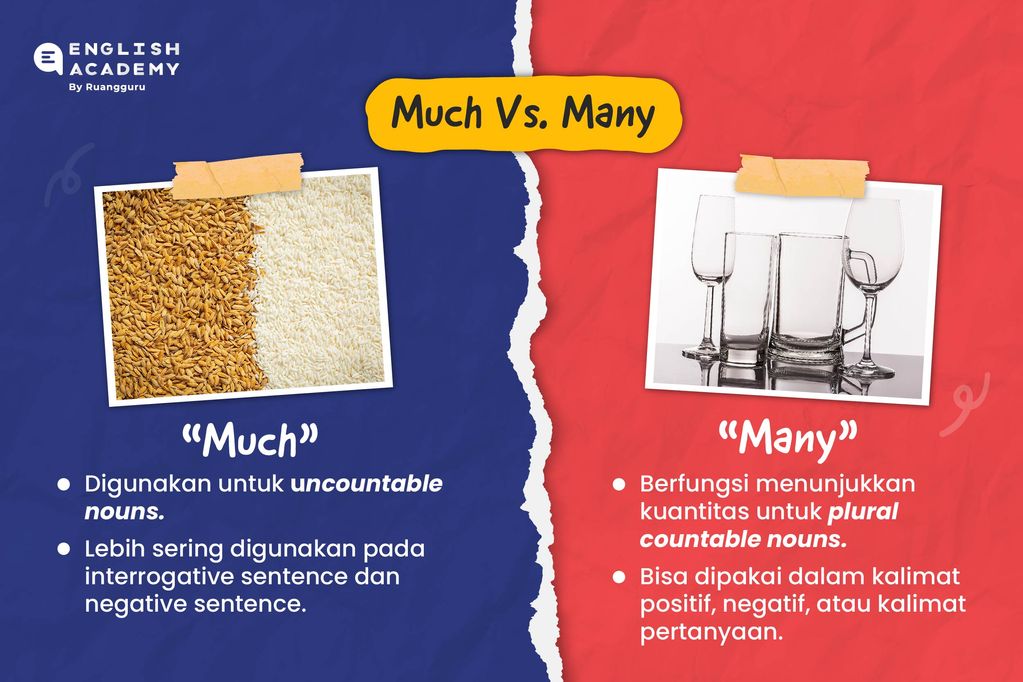
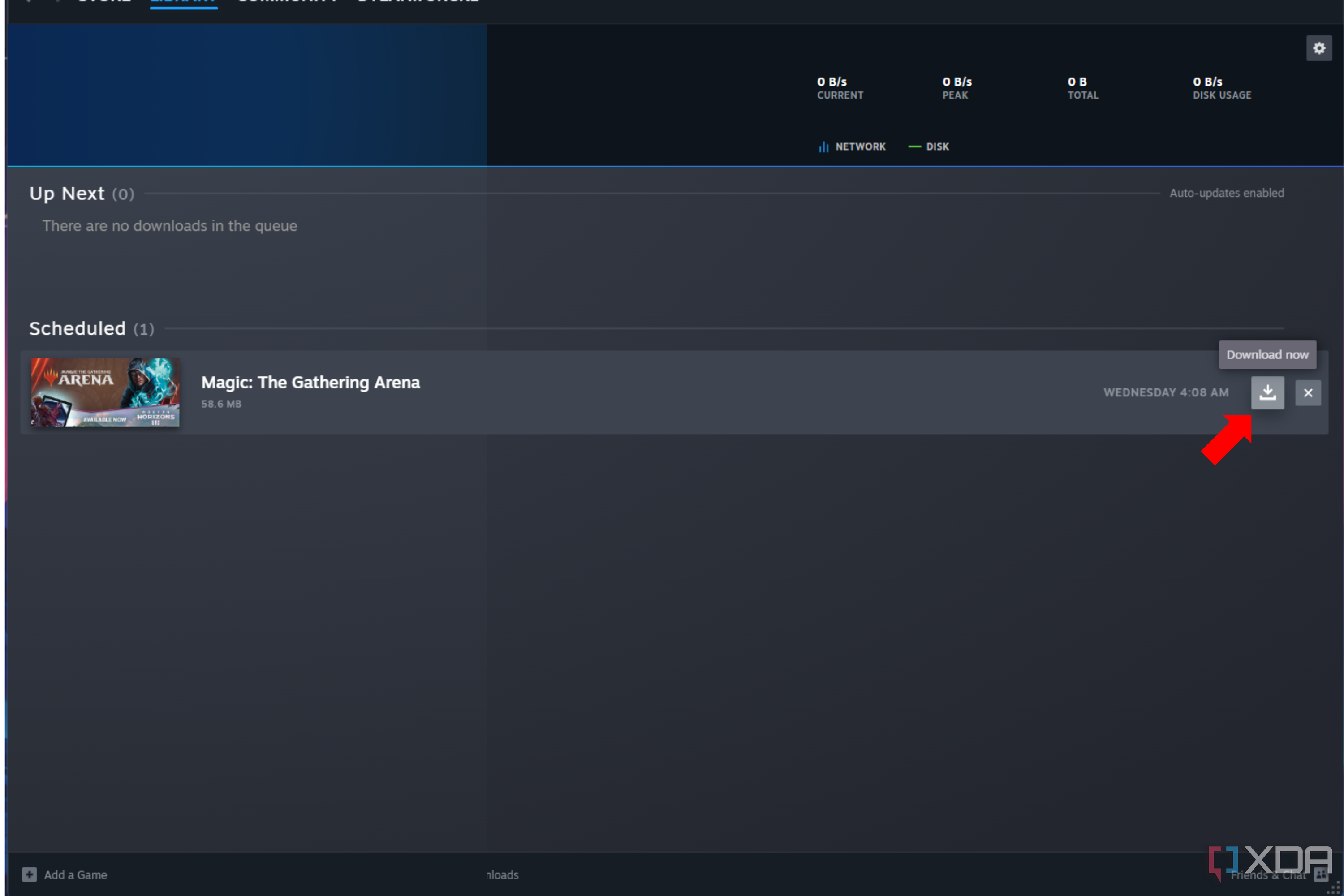
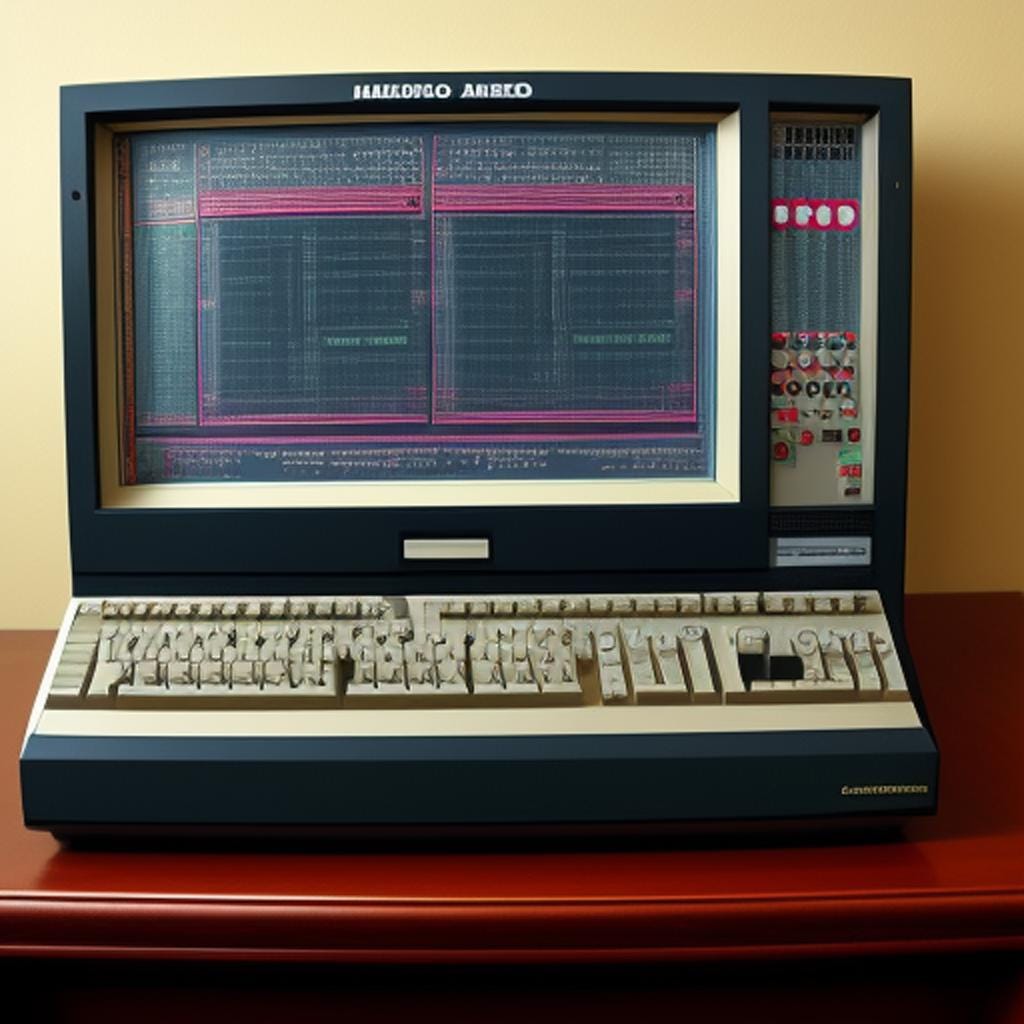
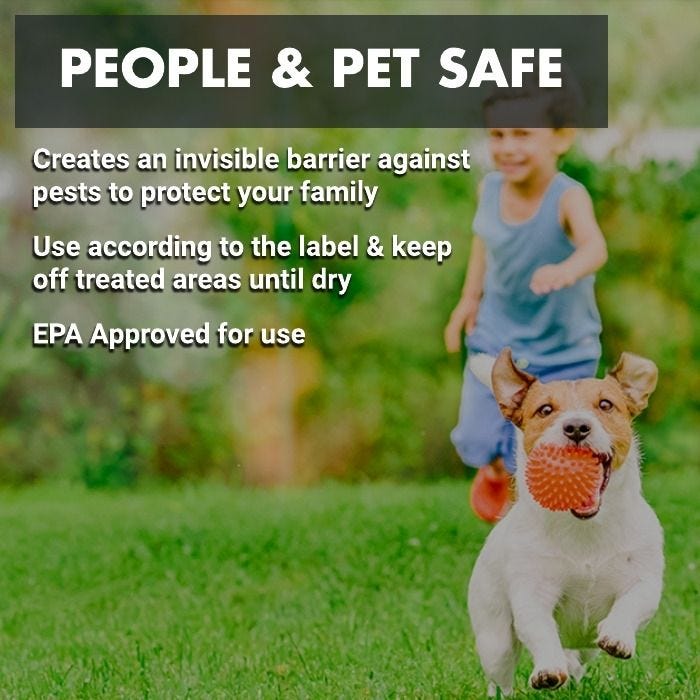
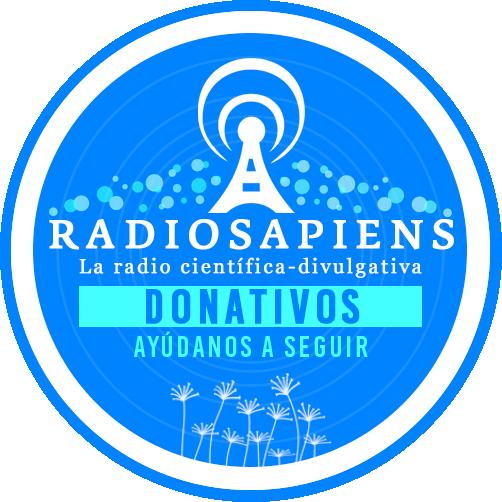
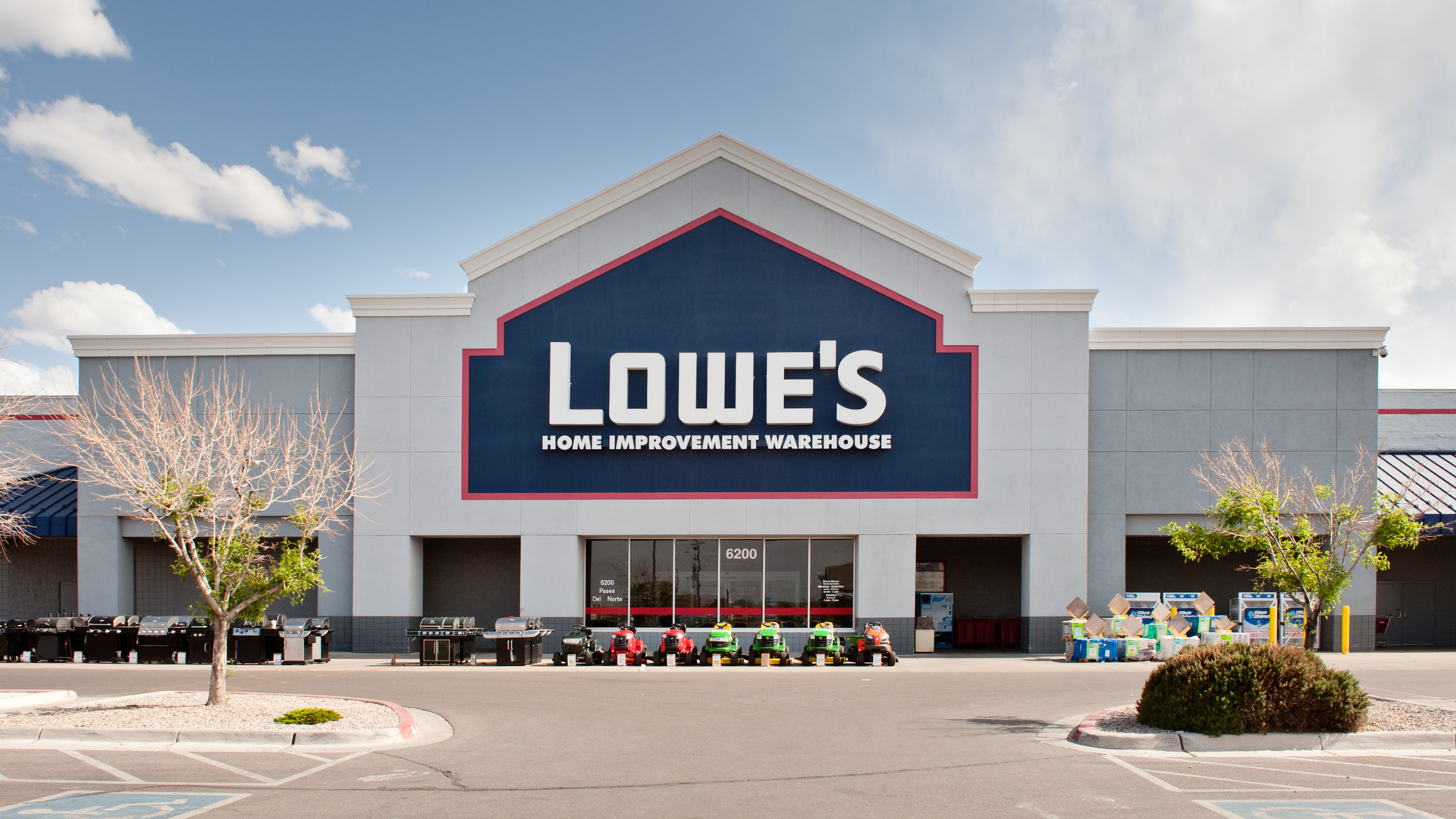
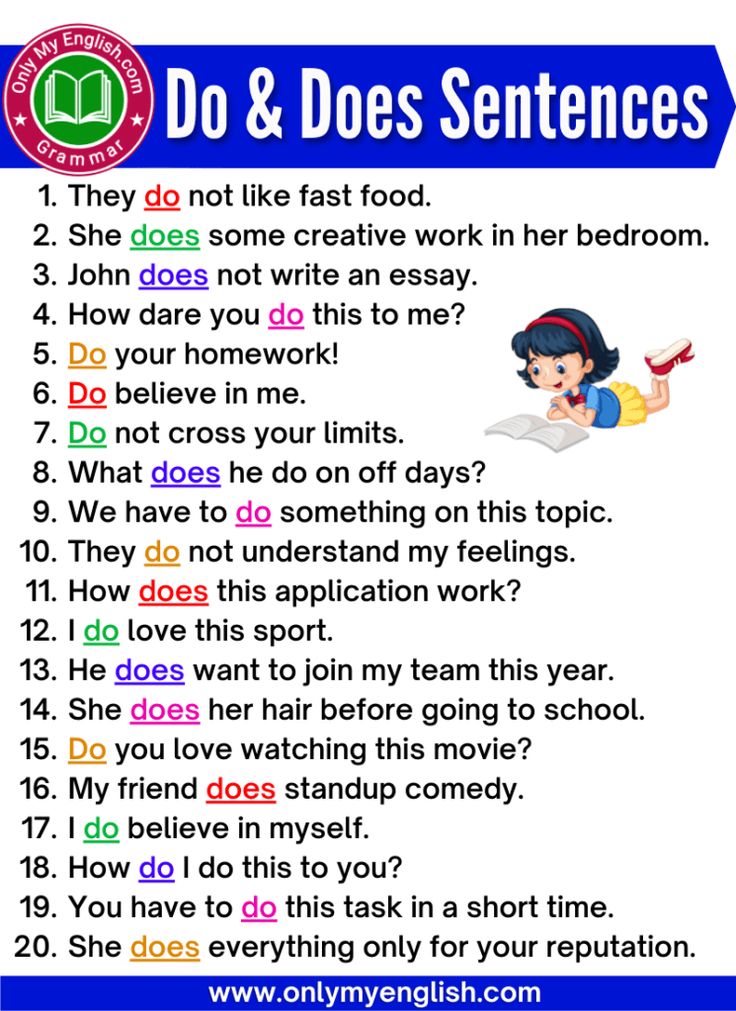
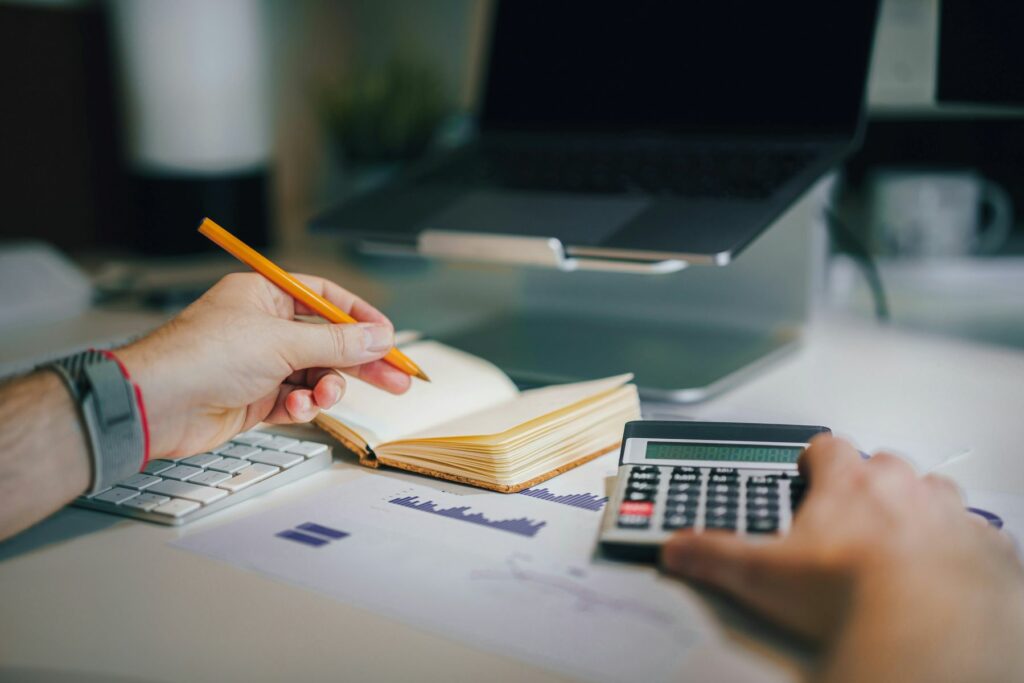
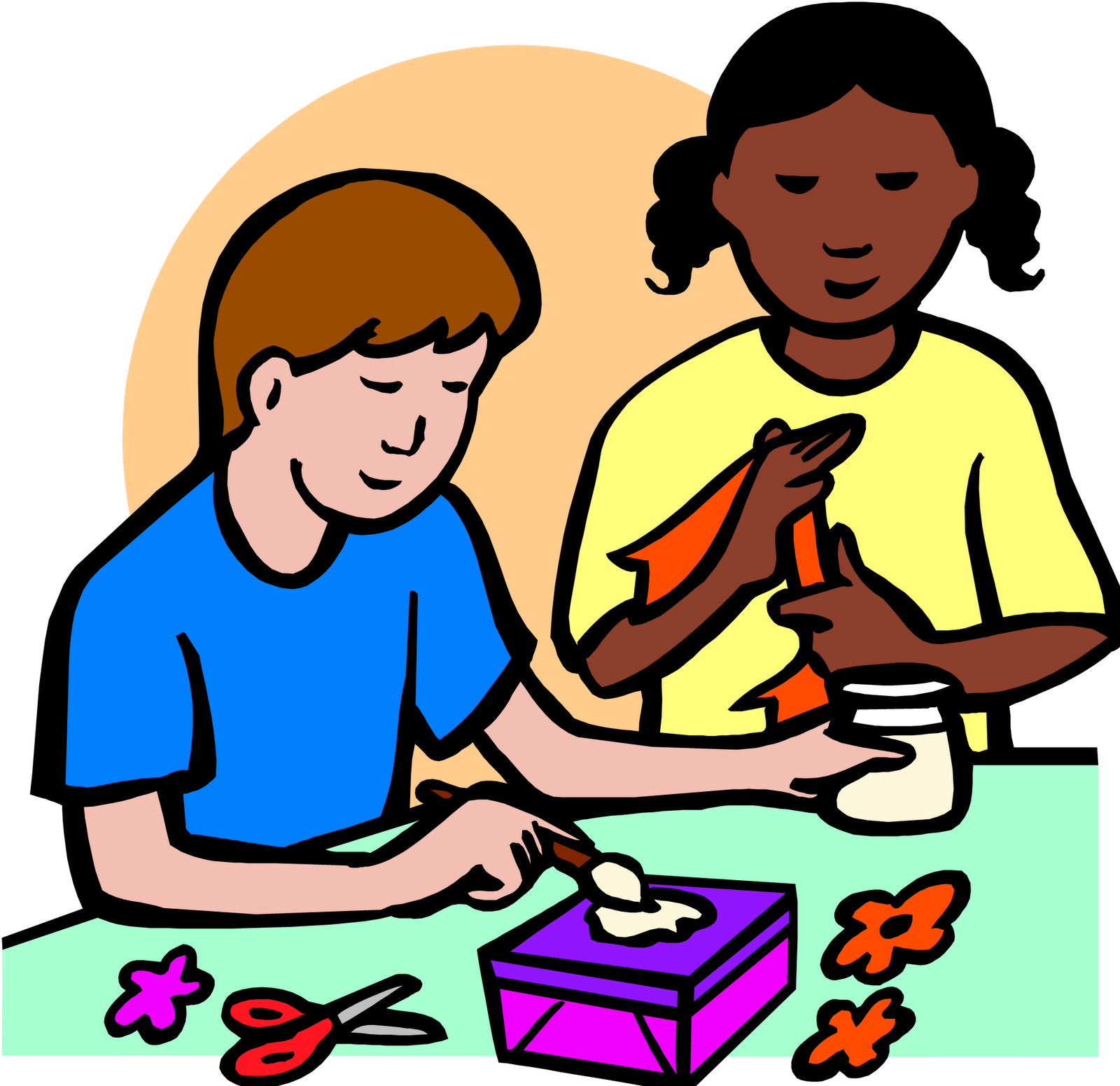
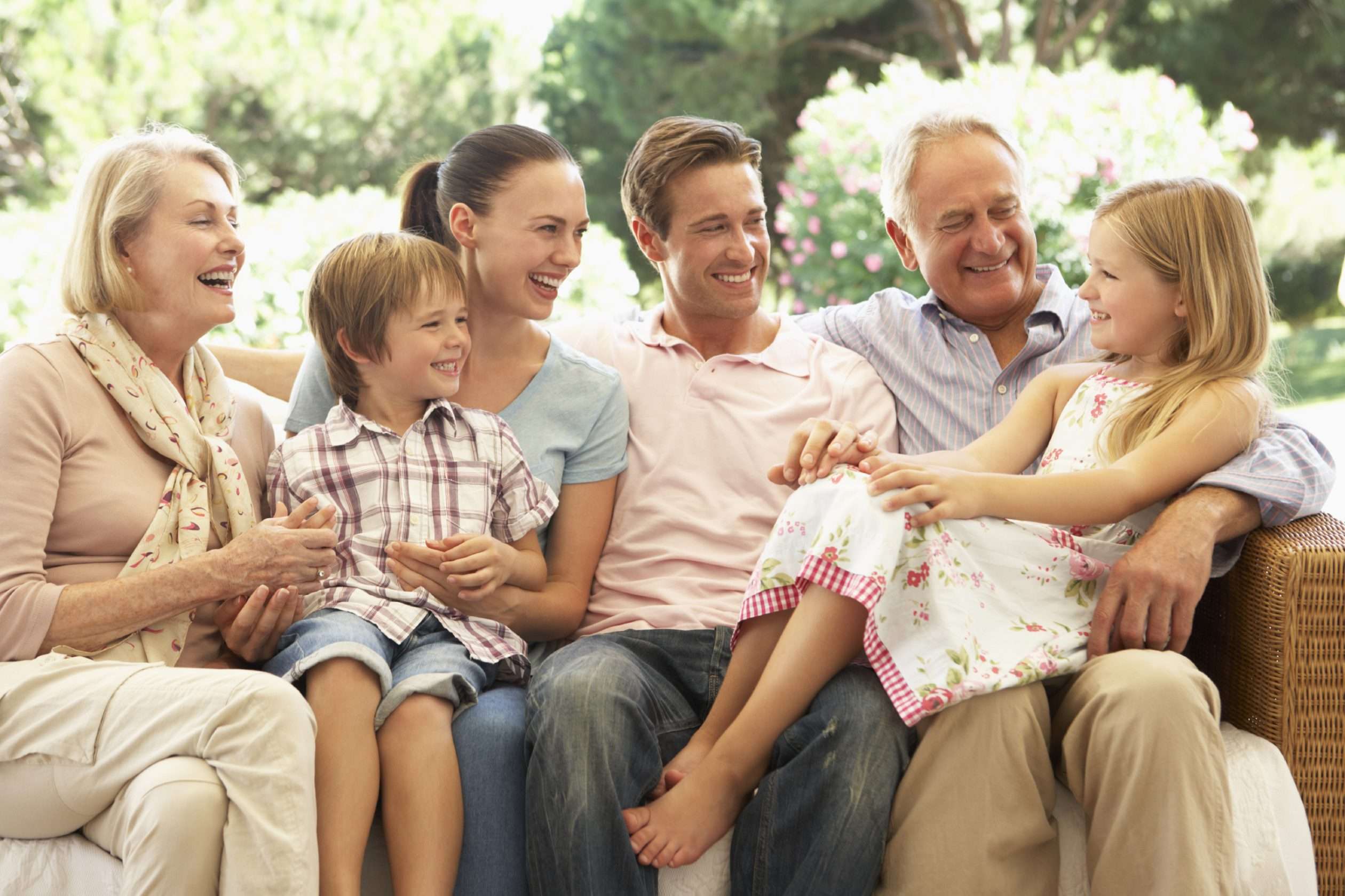
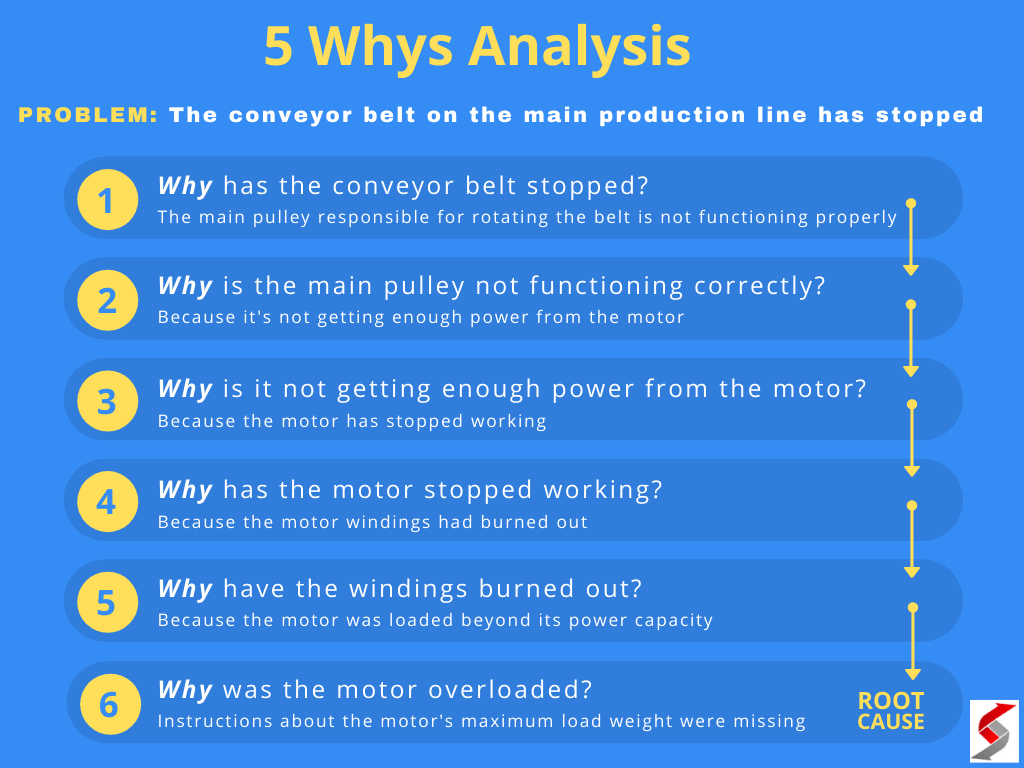