Automotive CAN Bus Diagnostics: Essential Guide to Testing and Troubleshooting
Understand automotive can bus systems
The controller area network (can) bus has revolutionized vehicle electronics since its introduction by Bosch in the 1980s. Modern vehicles contain dozens of electronic control units (ecus) that communicate through this digital network, eliminate the need for complex point to point wiring harnesses. This sophisticated communication protocol has become the backbone of automotive electronics, handle everything from engine management to comfort features.
Can bus technology allow multiple microcontrollers to communicate without a host computer. This distributes control system create a robust network where messages are broadcast to all connect devices. Each message contain an identifier that help receive devices determine whether to process or ignore the data. This elegant solutionreducese wiring complexity while increase reliability and functionality.
Why can bus diagnostics matter
As vehicles become progressively computerized, the ability to diagnose can bus issues has become essential for automotive technicians. When the can bus system malfunctions, it can trigger multiple apparently unrelated warning lights, create intermittent electrical problems, or cause complete system failures. These symptoms can be challenge to trace without proper diagnostic tools and knowledge.
Effective can bus diagnostics allow technicians to:
- Identify communication failures between modules
- Detect wiring issues such as shorts or open in the network
- Monitor real time data transmission between components
- Verify proper network termination resistance
- Isolate problematic ecus without extensive disassembly
Without these capabilities, technicians might resort to replace expensive components unnecessarily or miss the root cause wholly.
Essential can bus diagnostic tools
Professional grade can bus testers
Professional can bus testers provide comprehensive analysis capabilities for automotive technicians. These specialized tools typically offer features like signal quality measurement, error frame detection, and detailed protocol analysis. Many can capture and decode can message in real time, allow technicians to observe communication patterns between ecus.
High end can bus analyzers oftentimes include:
- Multichannel oscilloscope functionality
- Protocol decode for various can variants (include can fFD)
- Automated network health testing
- Statistical analysis of bus traffic
- Trigger capabilities for capture specific events
These professional tools represent a significant investment but provide the virtually detailed diagnostic information for complex network issues.
Old ii scan tools with can capabilities
Many modern old ii scan tools incorporate can bus diagnostic features. While not angstrom comprehensive as dedicated can analyzers, these tools provide sufficient functionality for many diagnostic scenarios. They connect to the vehicle’s diagnostic port and can read diagnostic trouble codes (dDTS))display live data streams, and oft perform basic network tests.
When select an old ii tool for can diagnostics, look for features like:
- Support for multiple can protocols (iISO15765, sSAEj1939, etc. )
- Ability to access multiple control modules
- Bidirectional control capabilities
- Graph functions for data analysis
- Software update to maintain compatibility with newer vehicles
These versatile tools serve as the first line of diagnostic equipment for most automotive technicians.
DIY can bus testing solutions
For enthusiasts or technicians on a budget, several DIY options exist for basic can bus testing. Arduino or Raspberry Pi base solutions with appropriate can interface can monitor bus traffic and perform basic diagnostics. Open source software like ccontactor ssavvy canprovide the interface for analyze capture data.
While these DIY solutions lack the polish and comprehensive features of commercial tools, they can efficaciously:
- Monitor can traffic in real time
- Log messages for later analysis
- Detect basic communication errors
- Send test messages to the network
These approaches require more technical knowledge but provide an affordable entry point into can diagnostics.
Can bus testing procedures
Physical layer testing
The physical layer represents the actual electrical signals and wiring of the can network. Test this layer involve verify proper voltage levels, termination resistance, and signal integrity. A digital multimeter and oscilloscope are essential tools for these measurements.

Source: GMAC fieldbus.com
Key physical layer tests include:
- Measure termination resistance (should be roughly 60 ohms when measure across can hhigh-pitchedand can low with the vehicle power off )
- Check for shorts to power, ground, or between can high and can low
- Verify proper signal voltage levels (can high should reach around 3.5v and can low around 1.5v during transmission )
- Examine signal quality for issues like reflections or excessive noise
Physical layer problems oftentimes cause intermittent communication issues that can be difficult to diagnose without proper measurements.
Data link layer testing
The data link layer concerns the transmission of data frames on the network. Test this layer involve monitor message traffic, identify error frames, and verify proper communication protocols. Can analyzers excel at this type of testing.
Important data link tests include:
- Monitoring error frame count (excessive error frames indicate problems )
- Verifying expect message IDs are present on the network
- Check message timing and frequency
- Test for proper acknowledgment of transmit messages
Data link issues oftentimes manifest as communication timeouts or miss functionality in vehicle systems.
Network layer diagnostics
Network layer diagnostics focus on the overall health and performance of the can network. This includes analyze bus load, identify bandwidth issues, and test gateway functionality between different networks.
Effective network diagnostics involve:
- Measure bus utilization (excessive bus load can cause message delays )
- Test gateway functionality between different vehicle networks (can, lLin fflex ray etc.)
- Verify proper message routing between network segments
- Check for message collisions or arbitration issues
Network layer problems typically affect multiple systems and may cause ostensibly unrelated symptoms across the vehicle.
Common can bus failure modes and their diagnosis
Open circuit conditions
Open circuits in can wire represent one of the wewell-nighommon failure mode. When a can wire breaks or disconnects, it ininterruptsommunication for all devices downstream of the break. Diagnose open circuits require systematic testing of the network segments.
Diagnostic approach:
- Measure termination resistance across can high-pitched and can low (an open circuit oft show higher than normal resistance )
- Use a time domain refractometer (tTDR)or similar technology to locate the position of the break
- Disconnect modules consecutive to isolate the problematic segment
- Inspect high flex areas and connection points where breaks usually occur
Open circuits typically cause complete communication failure for affected modules.
Short circuit failures
Short circuits occur when can high or can low wires contact each other, ground, or power. These conditions prevent proper signal transmission and can potentially damage connect modules. Shorts require immediate attention to prevent further damage.
Diagnostic steps:
- Measure resistance between can high / low and vehicle ground (should be high impedance )
- Check for voltage on can line with the vehicle power on ((nexpected voltage indicate a short to power ))
- Look for physical damage to wiring, specially in areas subject to heat, vibration, or moisture
- Test for intermittent shorts by flex wiring harnesses while monitor signals
Short circuits oftentimes trigger multiple DTS across various modules and may cause fuse failures.
Signal integrity issues
Signal integrity problems occur when the can signals are present but degrade by electrical noise, impedance mismatches, or improper termination. These issues cause intermittent communication errors that can be challenge to diagnose.
Diagnostic techniques:
- Use an oscilloscope to observe signal quality, look for ringing, noise, or irregular waveforms
- Check for proper termination resistance at both ends of the network
- Verify shield continuity and proper grounding if the network use shielded cable
- Test for external interference sources by operate the vehicle in different environments
Signal integrity issues typically cause intermittent problems that worsen under specific operating conditions.
Advanced can bus diagnostic techniques
Passive monitoring and analysis
Passive monitoring involve connect to the can bus and observe message traffic without interfere with normal operation. This non-intrusive approach allow technicians to baseline normal network behavior and identify anomalies.
Effective passive monitoring include:
- Record message patterns during various vehicle operations
- Analyze message timing and frequency
- Identify miss or unexpected messages
- Correlate message patterns with vehicle symptoms
This technique prove peculiarly valuable for intermittent issues that solely occur under specific conditions.
Active testing and simulation
Active testing involve send test messages to the can bus or simulate module behavior. This approach allow technicians to verify module responses and isolate problematic components without replace parts.
Active testing methods include:
- Transmit specific message IDs to trigger module responses
- Simulate sensor input to verify proper system reactions
- Perform module substitution tests use know good components
- Create control error conditions to test system fault tolerance
Active testing require careful implementation to avoid trigger unintended vehicle responses.
Gateway and multi network diagnostics
Modern vehicles oft contain multiple networks (can, lLin fflex ray Ethernet) interconnect through gateway modules. Diagnose issues across these networks require specialized tools and techniques.
Multi network diagnostic approaches include:
- Test gateway modules for proper message translation and route
- Verify synchronization between different network types
- Analyze timing relationships between inter network messages
- Isolate problems to specific network segments
Gateway issues oftentimes manifest as selective communication failures between systems on different networks.
Can bus tester selection guide
Key features to consider
Select the right can bus tester depend on your specific diagnostic needs and budget. Several key features differentiate various testing tools:
-
Protocol support:
Ensure the tool support all can variants use in your target vehicles (standard can, can fFD j1939, etc. ) -
Physical interface options:
Consider whether you need old ii connectivity, direct wire connection capabilities, or specialized interfaces -
Sampling rate:
Higher sampling rates provide more detailed signal analysis for physical layer testing -
Buffer depth:
Larger buffers allow longer record sessions for intermittent issue diagnosis -
Software capabilities:
Advanced filtering, triggering, and analysis features simplify complex diagnostics -
Updateability:
Regular software update ensure compatibility with newer vehicle systems
The ideal tester balances these features against cost constraints for your specific application.
Budget options vs. Professional equipment
Can bus testing equipment spans a wide price range, from basic DIY solutions under $100 to professional analyzers exceed $$10000. Understand the capabilities and limitations at different price points help make informed purchasing decisions.

Source: GMAC fieldbus.com
Budget options ($$100$500 ))
- Basic old ii scan tools with limited can monitor
- DIY solutions use microcontrollers and open source software
- Simple can adapters that require external software
Mid-range options ($$500$2,000 ))
- Advanced scan tools with enhanced can capabilities
- Entry level dedicated can analyzers
- Pc base systems with professional software
Professional equipment ($$2000 + ))
- Multichannel can analyzers with oscilloscope functionality
- Systems support multiple automotive networks simultaneously
- Tools with advanced trigger and automate testing feature
The appropriate investment level depends on diagnostic frequency, complexity of target vehicles, and require capabilities.
Best practices for can bus troubleshooting
Systematic diagnostic approach
Effective can bus troubleshooting require a methodical approach that progress from simple to complex tests. This systematic process helps identify the root cause expeditiously without unnecessary parts replacement.
A proven diagnostic sequence includes:
- Verify the complaint and identify affected systems
- Retrieve and analyze diagnostic trouble codes from all modules
- Check for technical service bulletins relate to the symptoms
- Test basic power and ground connections to affected modules
- Perform physical layer tests on can wire
- Monitor can communication during symptom occurrence
- Isolate the network segment or module cause the issue
- Repair or replace the faulty component
- Verify the repair resolve all symptoms
Follow this structured approach prevent misdiagnosis and unnecessary parts replacement.
Documentation and reference materials
Proper documentation importantly improves diagnostic efficiency. Maintain access to vehicle specific network diagrams, expect messageIDss, and normal signal parameters provide crucial reference information.
Essential reference materials include:
- Vehicle specific wiring diagrams show can network topology
- Module location and connector pinout information
- Expect resistance values and signal parameters
- Know good waveform captures for comparison
- Manufacturer specific diagnostic procedures
Build a personal reference library of these materials improve diagnostic speed and accuracy over time.
Training and skill development
Can bus diagnostics require specialized knowledge that develop through training and experience. Invest in ongoing education ensure technicians remain effective as vehicle technology evolve.
Valuable training resources include:
- Manufacturer specific technical training courses
- Aftermarket diagnostic equipment training
- Online forums and technical communities
- Industry publications focus on vehicle networks
- Hands on practice with know good and faulty systems
The virtually effective technicians combine theoretical knowledge with practical experience gain through systematic troubleshooting.
Future trends in automotive network diagnostics
Vehicle network technology continue to evolve quickly, with implications for diagnostic approaches and equipment. Several trends are shape the future of automotive network diagnostics:
-
Higher speed networks:
Can FD, automotive Ethernet, and other high bandwidth protocols require more sophisticated testing equipment -
Cybersecurity considerations:
Secure gateway architecture and encrypt communications create new diagnostic challenges -
Remote diagnostics:
Cloud connect diagnostic tools enable expert support and data analysis from anyplace -
Ai assisted troubleshooting:
Machine learning algorithms help identify patterns and suggest diagnostic approaches -
Integrated vehicle health monitoring:
Continuous network monitor systems detect issues before they cause failures
Stay current with these evolve technologies ensure diagnostic capabilities keep pace with vehicle complexity.
Conclusion
Effective can bus diagnostics represent an essential skill for modern automotive technicians. As vehicles progressively rely on complex networks for critical functions, the ability to test, analyze, and repair these systems expeditiously become fundamental to successful repairs.
By understand can bus principles, select appropriate testing equipment, and follow systematic diagnostic procedures, technicians can confidently tackle network relate issues that might differently seem insurmountable. The investment in proper tools and knowledge pay dividends through firm, more accurate diagnoses and reduce parts replacement costs.
As automotive technology continue its rapid evolution, maintain and expand can diagnostic capabilities ensure technicians remain effective in a progressively computerize vehicle environment. The foundations establish in this guide provide a starting point for develop these essential skills.
MORE FROM gowithdeal.com
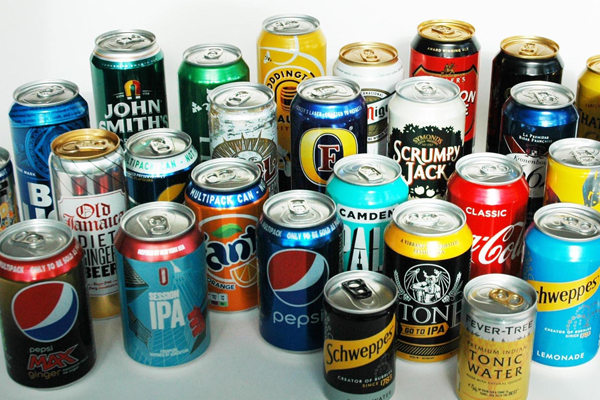
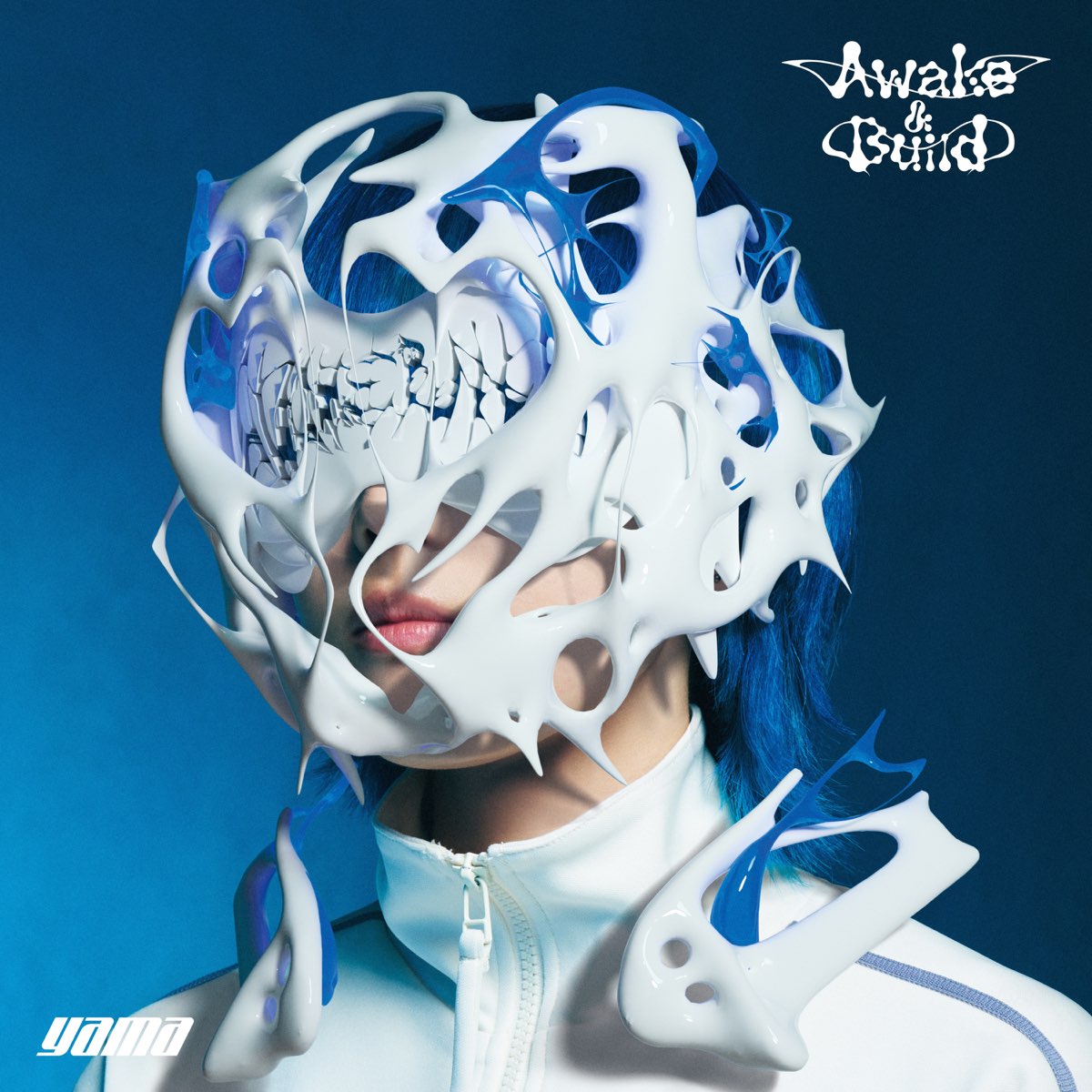
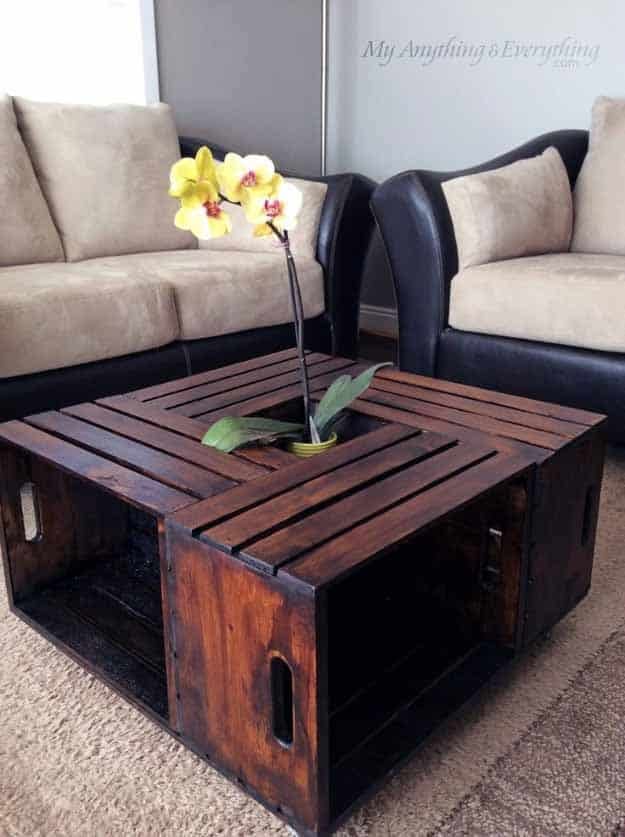
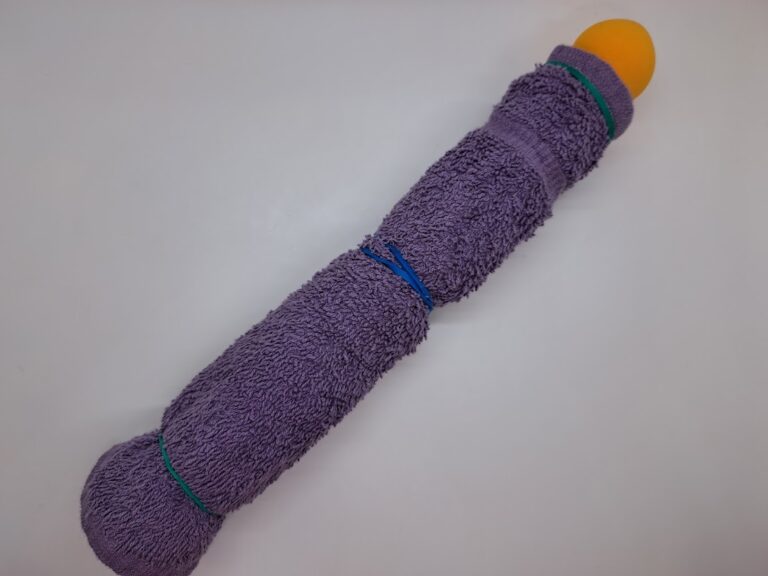
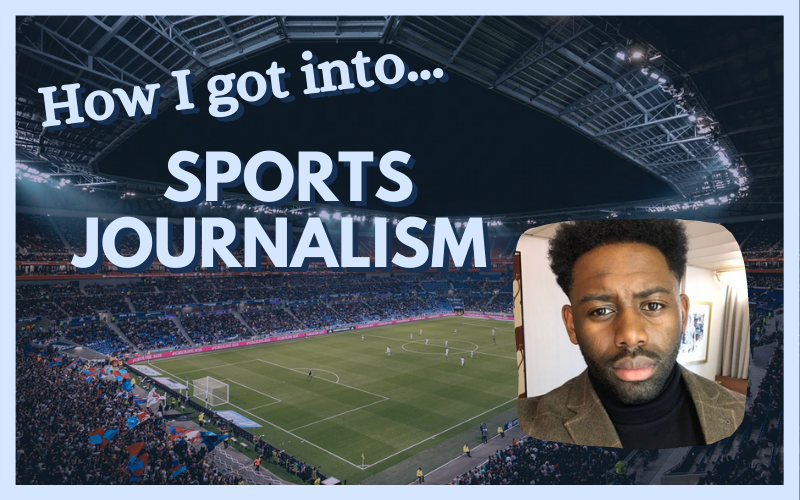
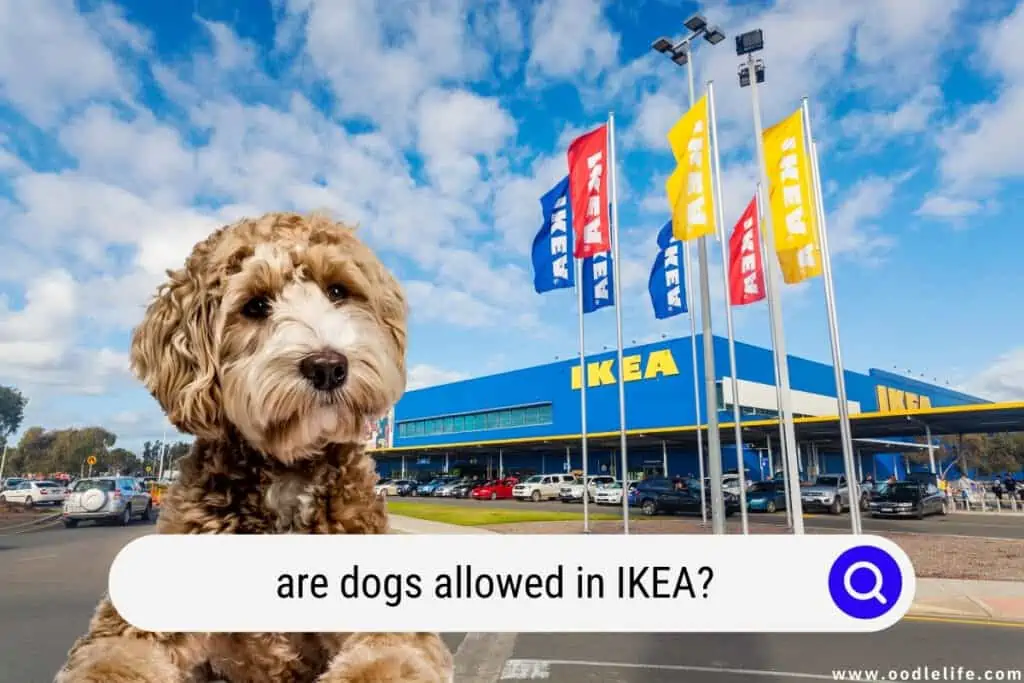
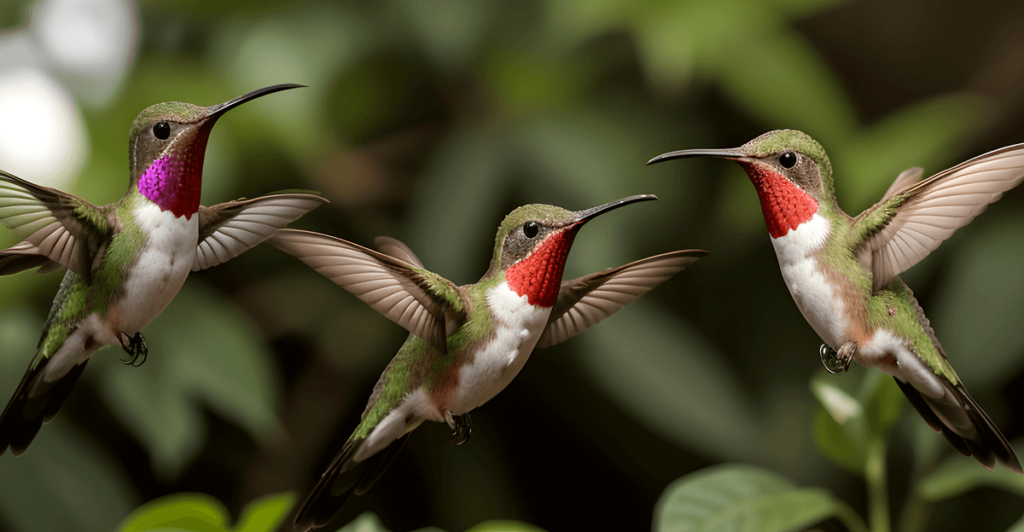
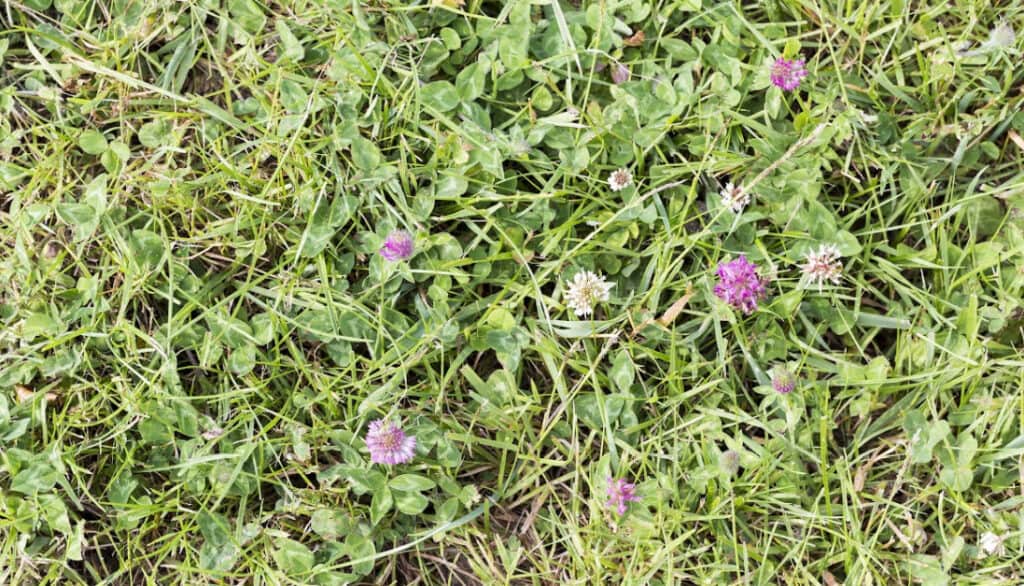
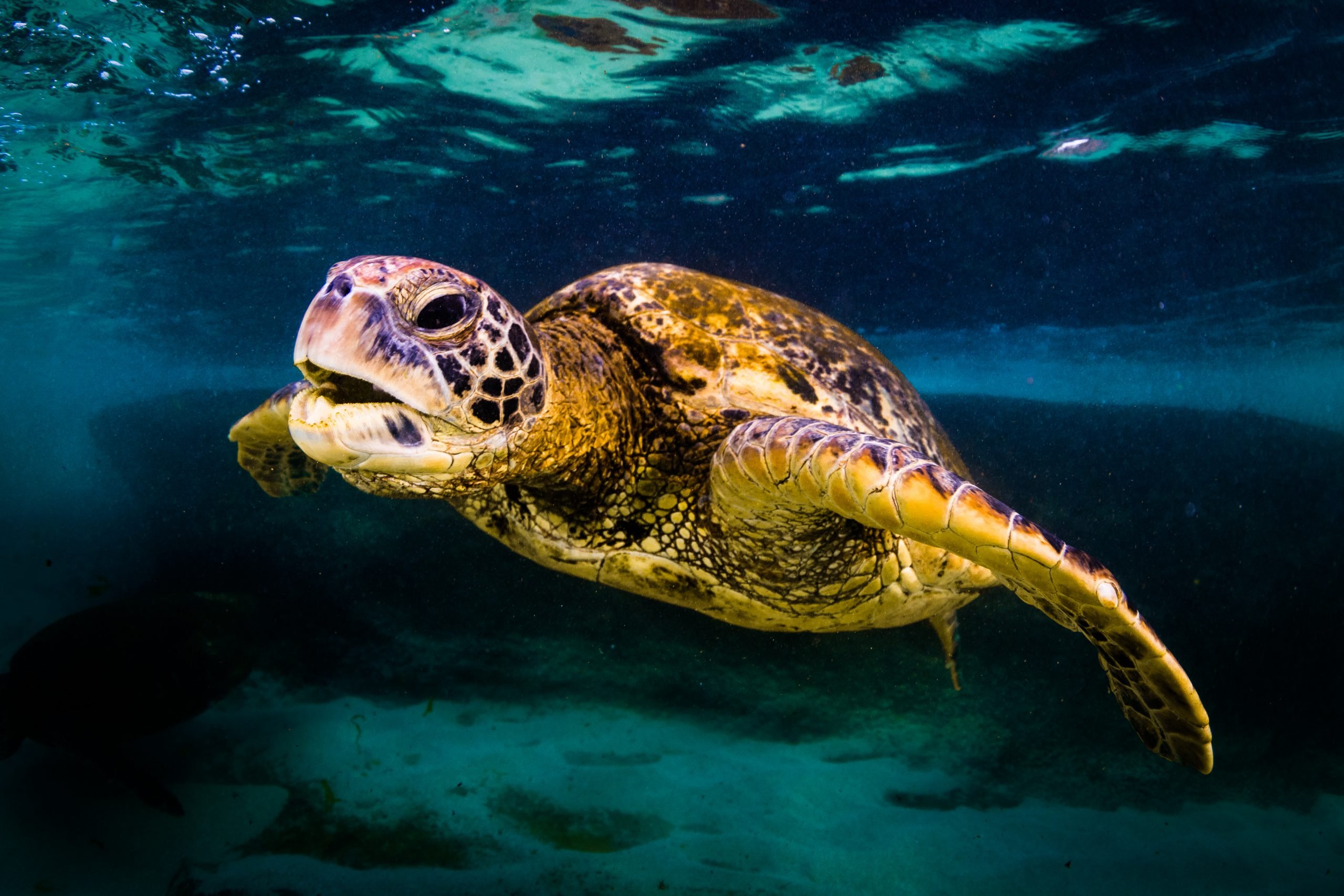
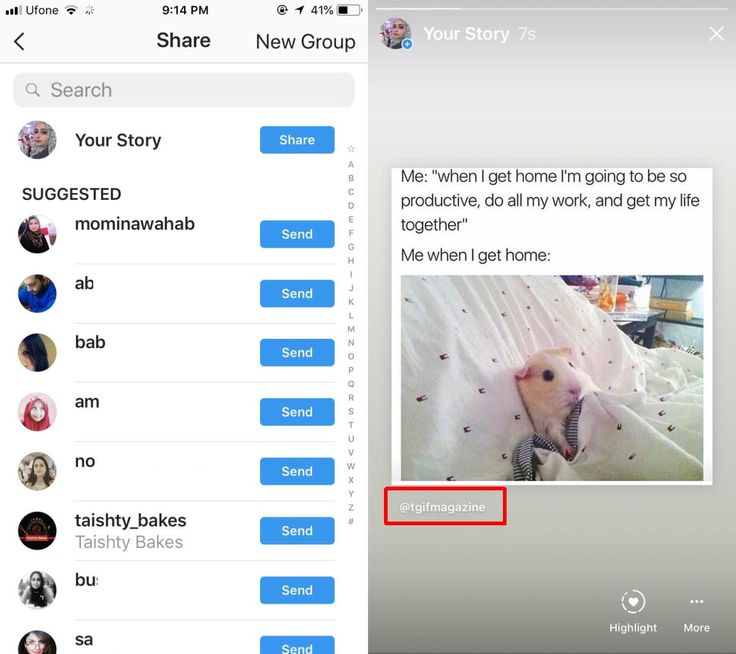
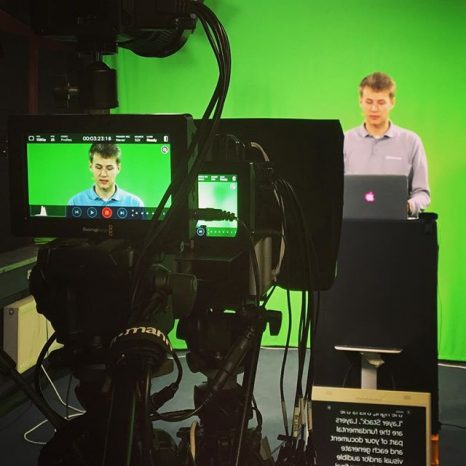
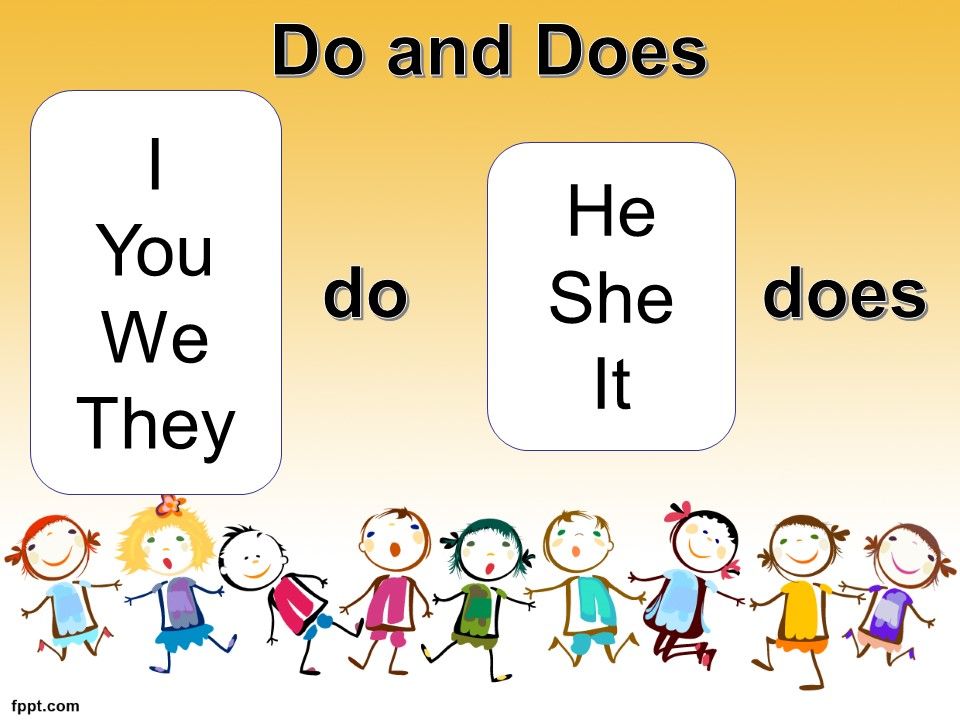